テクノロジー
技術レポート:アーカイブ
Category:FAトータルソリューション
製造管理業務を支援するシステムの開発事例紹介
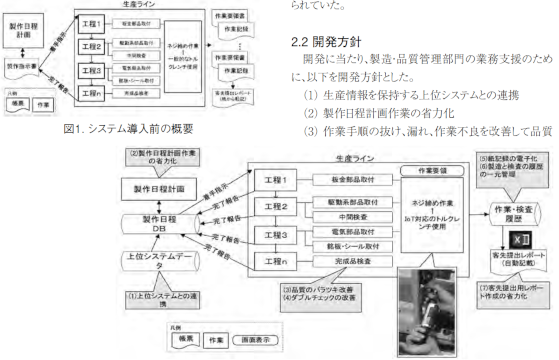
近年、当所の取引先では、工場での組立て工程における生産指示、実績管理のシステム化と生産プロセスのトレーサビリティを記録・分析するなどITを駆使したシステムへのニーズが高まっている。今回、手作業が多い組立て現場向けに、パソコンと通信可能なIoT工具を活用し、効率的な作業情報収集による作業品質の向上と製造管理業務の効率化などを目的とした製造管理システムを開発した。本稿では、製造管理システム全体の機能、改善点などを紹介する。
参考情報:
- この技術レポートは、当社が展開するFA・産業メカトロニクス事業のFAトータルソリューションに係る技術について著述されたものです。
- FAトータルソリューションは、トータルソリューション事業所が提供しています。
製造管理業務を支援するシステムの開発事例紹介 1. まえがき 近年、当所の取引先では、工場での組立て工程における生産指示、実績管理のシステム化と生産プロセスのトレーサビリティを記録・分析するなどITを駆使したシステムへのニーズが高まっている。今回、手作業が多い組立て現場向けに、パソコンと通信可能なIoT工具を活用し、効率的な作業情報収集による作業品質の向上と製造管理業務の効率化などを目的とした製造管理システムを開発した。本稿では、製造管理システム全体の機能、改善点などを紹介する。 2. 製造管理システムの概要 2.1 導入背景システム導入前の生産ラインの概要を図1に示す。図1. システム導入前の概要生産指示を製作指示書で行い、作業要領は作業要領書で示し、作業結果は作業記録で保管していた。さらに、客先提出用レポートは、品質管理者が作業記録から時間をかけて転記していた。また、管理業務の大部分が手作業で行われており、管理担当者の経験による技術に依存していた。生産する機種、部品点数、作業手順数は以下のとおり。(1) 機種:63種類(2) 部品点数:約80~120点/機種(3) 作業手順数:板金部品取付、駆動系部品取付、中間検査など、約400~600手順/機種多様な機種と作業手順の多さから、抜け、漏れ、作業不良による品質のバラツキがあった。また、作業の重要ポイントであるネジ締め作業の合否判断は、作業者と品質担当者によるダブルチェックを行っており、検査履歴も紙で記録・保管され、製造履歴との照合に時間がかかっていた。以上のことが、コスト増の要因となっていたため、改善が求められていた。2.2 開発方針開発に当たり、製造・品質管理部門の業務支援のために、以下を開発方針とした。(1) 生産情報を保持する上位システムとの連携(2) 製作日程計画作業の省力化(3) 作業手順の抜け、漏れ、作業不良を改善して品質製造管理業務を支援するシステムの開発事例紹介長崎事業所 技術第1部 情報制御システム課松本 宏図2. 製造管理システム導入による改善概要52製造管理業務を支援するシステムの開発事例紹介一般論文バラツキの改善(4) IoT工具を活用したネジ締め付け作業のチェック工数削減(5) 紙の作業記録、検査結果等の電子化(6) 製造と検査の履歴の一元管理による照合作業の効率化(7) 客先提出レポート作成作業の省力化改善イメージを図2に示す。以上の開発方針をもとに、開発した機能を表1に示す。表1. 機能一覧2.3 システム構成システム構成を図3に示す。アプリケーションとデータベースはサーバを分離しており、各サーバ及びパソコン、バーコードプリンタ、現品票プリンタは、構内ネットワークで通信する。また、パソコンとネジ締め作業に使用するトルクレンチは、Bluetoothで適正トルク値制御の通信を行う。図3. システム構成図2.4 ソフトウェア構成ソフトウェア構成を図4に示す。本システムは、クライアントサーバ方式を採用した。アプリケーションサーバ側は、上位システムから生産情報の取り込みを行うとともに製造管理システム本体を実装する。クライアントパソコン側には、レポート出力ライブラリー、音声合成ライブラリーを実装する。データは、全てデータベースサーバに格納する。図4. ソフトウェア構成図3. 各機能の概要と特長、改善点3.1 上位システム連携と工程計画機能3.1.1 機能概要上位システム連携と工程計画機能の概要を図5に示す。工程計画機能は、主に作業共有情報の表示機能と、製作日程計画の自動割り付け計算機能で構成されており、以下に各機能の概要を説明する。(1) 上位システムとの連携上位システムに登録されている機種、製作台数、納期等の生産情報を始業前のバッチ処理で本システムに取り込み、基本情報入力の手作業を不要としている。(2) 製作日程計画の自動割り付け計算1台目の着手日を指示するだけで、1台目から全台数分について、自動で着手日時と完了日時を割り付け計算する。(3) 作業共有情報の表示製品仕様、設置場所など製造品ごとの情報をシステムに画面表示して、管理者と作業者で情報共有できるようにしている。53製造管理業務を支援するシステムの開発事例紹介3.1.2 特長(1) 製作日程計画の計算方法と手動調整機種別に工程ごとの作業時間をマスタ登録し、1日の製作能力工数をもとに、完了日を基準に製作日程の計算を行う。さらに、能力工数を変更し、残業などの調整を可能にした。日程計算結果は、着手日時、完了日時で保持しており、これらを変更することで手動での日程調整や、製作日程の再計算が可能である。これにより工程計画を容易にできるようにした。(2) 計画ミスの防止前工程との輻輳や着手済工程は調整を不可にする制限などを組み込み、物理的に無理な工程計画をできないようにした。図5. 上位システム連携と工程計画機能概要図3.2 作業ナビゲーション機能3.2.1 機能概要(1) 作業要領表示の支援製品に添付している現品票の製造番号をスキャンして作業を開始すると、図6に示す作業ナビゲーション画面に、電子化された作業要領書を表示する。品質不良が発生しやすい作業の注意事項などが表示されており、音声でも案内される。この指示を受けて作業を行う。作業内容に応じて、作業結果の自動チェックと目視確認チェックを選択して記録する。これにより、抜け、漏れ、作業不良の発生を削減した。(2) IoTに対応したトルクレンチの使用ネジ締めに使用する工具に、締め付け時のトルク値をパソコンに取り込める機能とパソコン側からトルクレンチ側に使用可否を設定できる機能があるものにした。(3) チェック作業の省力化トルク値をシステムが判断し、2人目の締め付け不良チェック作業を不要としている。さらに、作業結果、検査結果をシステムに登録することで、紙へ記録する作業も不要としている。図6. 作業ナビゲーション画面3.2.2 特長(1)トルクレンチの実績データの利用作業手順に従ってトルクレンチの締め付け実績データを記録するとともに作業結果判定を行うようにした。さらに締め付けデータの履歴には、不良結果も記録して、不良発生状況を分析できるようにしている。また、作業結果判定で不良があった場合に、品質管理者のポケットベルに送信するとともに、作業の稼働状態を示す三色表示灯を使用して障害発生の意味を持たせた赤色を点灯させるようにした。図7に作業ナビゲーション機能構成図を示す。54製造管理業務を支援するシステムの開発事例紹介図7. 作業ナビゲーション機能構成図(2) ネジ締め作業の品質向上作業ナビゲーション画面で、ネジ締め箇所と作業上の注意事項を指示し、ネジの種類、材質に応じて、図8のトルクレンチ制御シーケンスの順に、①トルクレンチへ適正トルク値範囲を送信する。②受信したトルクレンチは、ネジ締め中に適正トルク・トルク不足・トルクオーバーの3種類を点灯色と音で知らせ(図9参照)、適正トルク値で完了するように促す。③適正トルク値で、締め付け本数が一致する場合は、合格と判定し工具を使用不可にして手順を完了する。④不合格と判定した場合は、警告を表示して品質管理者をポケットベルで呼び出す。⑤品質管理者は、作業不良に対して原因・処置を指示する。このようにすることで、問題発見から対応までを見える化して、作業品質のバラツキをなくした。(3) 作業手順表示による作業品質の向上複雑な作業や作業注意事項など、確認が必要な作業手順を画面表示することで、作業漏れと連絡ミスを防止するようにした。(4) 作業者への伝達方法音声合成ライブラリーを使用し、作業指示内容や警告メッセージを画面表示だけでなく、音声でも知らせるようにした。また、各作業場所の運転状況について、稼働中、停止中、障害発生を三色表示灯で知らせるようにした。3.3 進捗管理機能3.3.1 機能概要(1) 進捗状況表示ネジ締め作業等の各工程の実績情報を収集し、計画に対する進捗度を表示する。(2) 進捗ステータスの設定進捗管理を行う上で、表2に示す4つの進捗ステータスを設定し、図10に示す3つのポイントで収集し、各工程の完了状況を確認できるようにしている。表2. 進捗ステータス一覧表図9. トルクレンチの締め付け状況の報告図8. トルクレンチ制御シーケンス図図10. 進捗管理の管理ポイントとタイミング図55製造管理業務を支援するシステムの開発事例紹介3.3.2 特長(1) 着手日確定ステータスの導入日程計画後に進捗状況に応じて工程調整を行い、最終決定した着手日を作業者に知らせる情報として導入した。着手日決定の条件の1つである部品揃えの状況は、上位システムのオーダー番号(注1)で手配した部品と製造番号を連携させ、容易に見えるようにした。(2) 着手中・完了済ステータスの導入作業ナビゲーションには、作業手順ごとの作業実績が記録されている。この情報を各工程の完了を判定する情報として利用した。これにより、リアルタイムに作業実績の収集と作業手順の未完了有無を容易に把握できるようになった。3.4 稼働状況表示機能3.4.1 機能概要(1) 稼働状況のリアルタイム表示工程計画及び作業ナビゲーションの作業実績により、稼働状況をリアルタイムに表示する。図11に示すように、計画と実績の情報を進捗管理者に見せる進捗管理者用、製造ラインの作業者に見せる製造ライン用に分けて、グラフ表示することで、状況把握を容易にしている。図11. 稼働状況表示画面3.4.2 特長(1) 稼働状況の見える化計画と実績を1か月単位、日単位、作業場所単位の3種類で確認できるようにした。また、進捗表示PC、作業者用PCでは、当日の目標生産台数と実績生産台数を表示するとともに、作業ナビゲーション画面にも作業ごとの目標作業時間のバーを表示して、作業者に進捗を意識させ、期限の遵守率を向上するようにした。(2)作業時間のバラツキの見える化同一工程やステーションごとの作業時間のバラツキをグラフでリアルタイムに表示し、進捗状況悪化の際に、要因分析対象の絞り込みを容易にした。3.5 トレーサビリティ機能3.5.1 機能概要(1) 作業履歴の一元管理製造品の出荷後に最終顧客やメンテナンス担当者から問合せがあった場合に、製造番号から製造履歴を検索できるようにしている。製造履歴には、使用部品のシリアル番号、作業実績、検査結果、作業担当者などがある。(2) 客先提出レポートの出力作業実績、検査結果などの情報から、客先提出用のレポートを出力する。3.5.2 改善点(1) 管理キーの統一による履歴管理の簡略化図12に示すとおり、従来は、出荷前と出荷後で製造品を識別する管理情報が異なっていた。そのため、出荷後の問合せには、製造番号から製作オーダー番号を確認する必要があり手間を要していた。これを見直し、工程計画段階から製造番号を付与することで、作業現場でも製造番号で管理するよう変更した。図12. 製造履歴の管理キー比較図(注1 ) 生産指示を識別するもので、品目、数量、納期などの情報を持つキーとなる番号。56製造管理業務を支援するシステムの開発事例紹介図13に示すとおり、管理キーの見直しにより、出荷時の管理を生産時と同様に、製作オーダー番号で実施することにより、生産から出荷までを同じキーで一貫して管理できるようになった。図13. トレーサビリティ機能のテータ連携図4. むすび本システムは、客先とともに改善の検討を行い、開発を進めた。作業分析・改善を繰り返して完成させたことで、作業者が確実に業務遂行できる状態を作ることができた。本システム稼働後は、作業品質のバラツキが改善し製品品質の向上と業務効率化に貢献しているとの客先評価を得ることもできた。今後も新技術、機器情報、ユーザーの要望を収集・検討し、さらに、設計力を強化するとともに、これまで培ったノウハウを活用し、ユーザーにとって効果的、効率的なシステムの開発を行っていく。最後に、本開発に当たり、貴重なご意見、ご指導をいただいた関係者の方々に深く感謝申し上げる。執筆者紹介松本 宏 マツモト ヒロシ1991年入社。主に業務系システムのソフトウェア開発に従事。現在、長崎事業所技術第1部情報制御システム課。57製造管理業務を支援するシステムの開発事例紹介