未来を拓くための技術PROJECT STORY_04
産業用ガス供給設備監視システム開発プロジェクト
半導体安定供給への貢献を通じて、
日本のモノづくりを支える。
PROLOGUE
産業用ガス供給設備監視システム開発プロジェクト
「産業の米」として、あらゆるモノづくりに不可欠な半導体。世界規模の半導体需要に対応するために計画された最新鋭の大規模半導体製造工場の立ち上げに際し、三菱電機ソフトウエアでは、製造工程で不可欠となる産業用ガスの供給設備監視システムを開発し、半導体の安定供給に大きく貢献した。それまでに実績のない大規模工場ならではの膨大な情報処理に耐えうるシステムに求められるものとは何か?そしてそれをどう乗り越えていったのか。中学の同級生でもあるプロジェクト責任者と現場の開発をリードするエンジニアに語ってもらった。
MEMBER
-
プロジェクト責任者
T.S
トータルソリューション事業所 営業部
営業第1課 課長(当時 監視制御システム課 課長)
1987年入社
工学部電気工学科卒 -
プロジェクトリーダー兼システムエンジニア
N.T
トータルソリューション事業所 長崎支所
技術第2部 監視制御システム課 主管
1985年入社
情報工学科卒
STORY
─本プロジェクトの概要について教えてください。
- T.S:
- デジタルカメラの普及に加え、高性能カメラを搭載したスマートフォンの普及が急速に広まったことなどから、CMOSイメージセンサーの需要が世界的に高まりました。これに伴って半導体に対する需要も世界的にひっ迫しており、半導体製造工場の新設が相次いでいることが背景にあります。
- N.T:
- 半導体製造には20数種類ものガスが使われており、正確かつ安全な供給は生産性向上の点でも不可欠な要素です。今回のプロジェクトは、そうした半導体製造工場向けにガスを供給する設備の監視システムを開発するものです。
- T.S:
- 私たちがシステムを提供したお客様は、半導体製造工場に産業用ガスを供給する産業用ガスメーカー様です。このお客様と協力しながらシステムを開発することで、半導体製造工場での適切なガス供給を可能にしました。
- N.T:
- プロジェクトの初期の頃、私はまだ参加していなかったのですが、提案がスタートしたのは2018年頃と聞いています。デモシステムの構築やシステム構成の提案等を経て採用が決定したのは、2020年でした。
- T.S:
- 今回のプロジェクトで用いたのは三菱電機のSCADA『GENESIS64™』です。SCADA(Supervisory Control And Data Acquisition)とはコンピュータによるシステム監視とプロセス制御を行う産業制御システムのことで、自動車や食品、薬品、化粧品などの製造業向けに生産ラインの制御システムや生産管理システムを提供してきました。この分野では40年ほどの長い歴史を誇り、十分な実績をもっています。
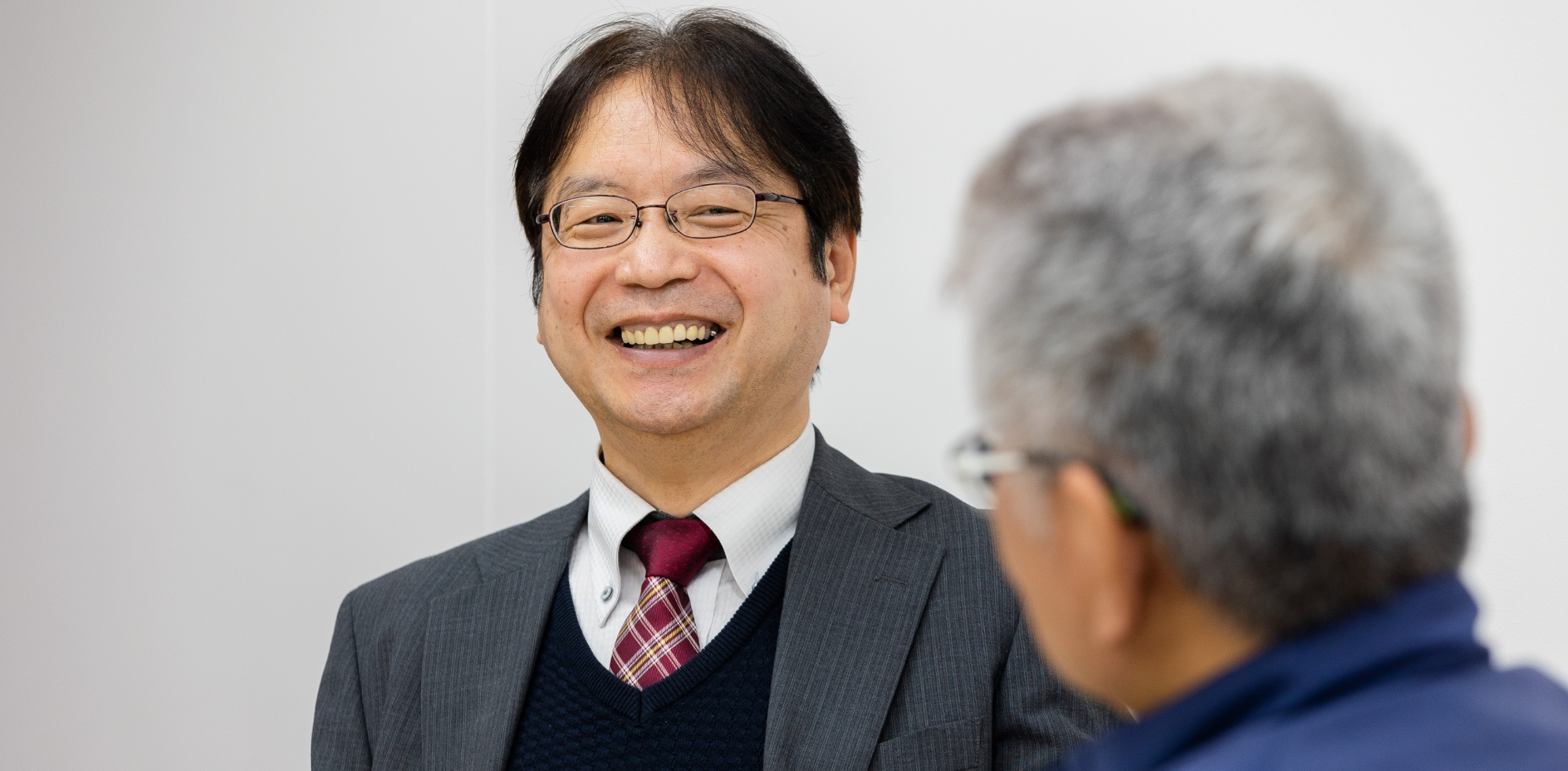
─プロジェクトが立ち上がった経緯について教えてください。
- T.S:
- そもそもは産業用ガスメーカー様からのお問い合わせがきっかけでした。同社では他の半導体工場に向けて産業用ガスの提供を行っていらっしゃいましたが、今回はそれをはるかに上回る大きな規模の案件に取り組むことになられたのです。
- N.T:
- 産業用ガスメーカー様が従来採用してきたシステムは6万点ほどのI/Oに対応したものでした。I/O点数とは、外部機器をコントロールするPLC(シーケンサ)と呼ばれる制御装置に接続される機器の点数のことです。今回のプロジェクトの対象となった新たな半導体工場では10万点を超えるI/O点数となることが見込まれ、従来のシステムでは対応できないことが判明。より大規模なシステムに対応可能なSCADAを検討される中で、三菱電機の『GENESIS64™』に注目されたわけです。
- T.S:
- 産業用ガスメーカー様はそれまで三菱電機グループとの接点は薄く、ネットで情報をリサーチした際に『GENESIS64™』を見つけられたとのことでした。そして三菱電機様に問い合わせがあり、当社が三菱電機グループとしてシステム開発に取り組むことになったわけです。
- N.T:
- とはいえ、これほど大規模なシステムにおける実績はなかったため、当初は不安もあったのですよね。
- T.S:
- そうなんです。このプロジェクトの話を耳にしたときは、ぜひ挑戦したいと思いました。その一方で10万点というI/O点数を聞き、それまでこれほどの規模での経験がなかったことから、本当に大丈夫だろうかと思ったのも事実です。
- N.T:
- そこでまずは検証のためのデモの狙いも含みつつ、「プロトタイプを製作させてほしい」と提案したわけですね。
- T.S:
- はい、性能面の検証と同時に、ユーザーが利用する画面の具体的なイメージを提案する意味もあって、プロトタイプの製作を行いました。10万点のI/O点数ともなると、データの処理速度や画面に表示される速度が大丈夫かという不安もありました。産業用ガスメーカー様は今回の半導体工場の案件を最重要案件に位置付けていると耳にしていたため、絶対に失敗は許されません。念には念を入れて検証しようという狙いがありました。
- N.T:
- 約1年の期間をかけ、プロトタイプとなるデモシステム製作を終え、無事にイメージした通りの成果が得られ、その結果を踏まえて正式受注へとつながったのですね。
- T.S:
- 『GENESIS64™』を用いたシステムが機能面、性能面において、今回の大規模システムにも十分対応できると証明されたわけです。最初の山を乗り越えることができて、ホッとしました。余談にはなりますが、このプロトタイプは産業用ガスメーカー様がお客様向けのデモンストレーション用に引き続き使ってくださっているそうです。お客様のビジネス拡大にもお役に立てているようで、嬉しいです。
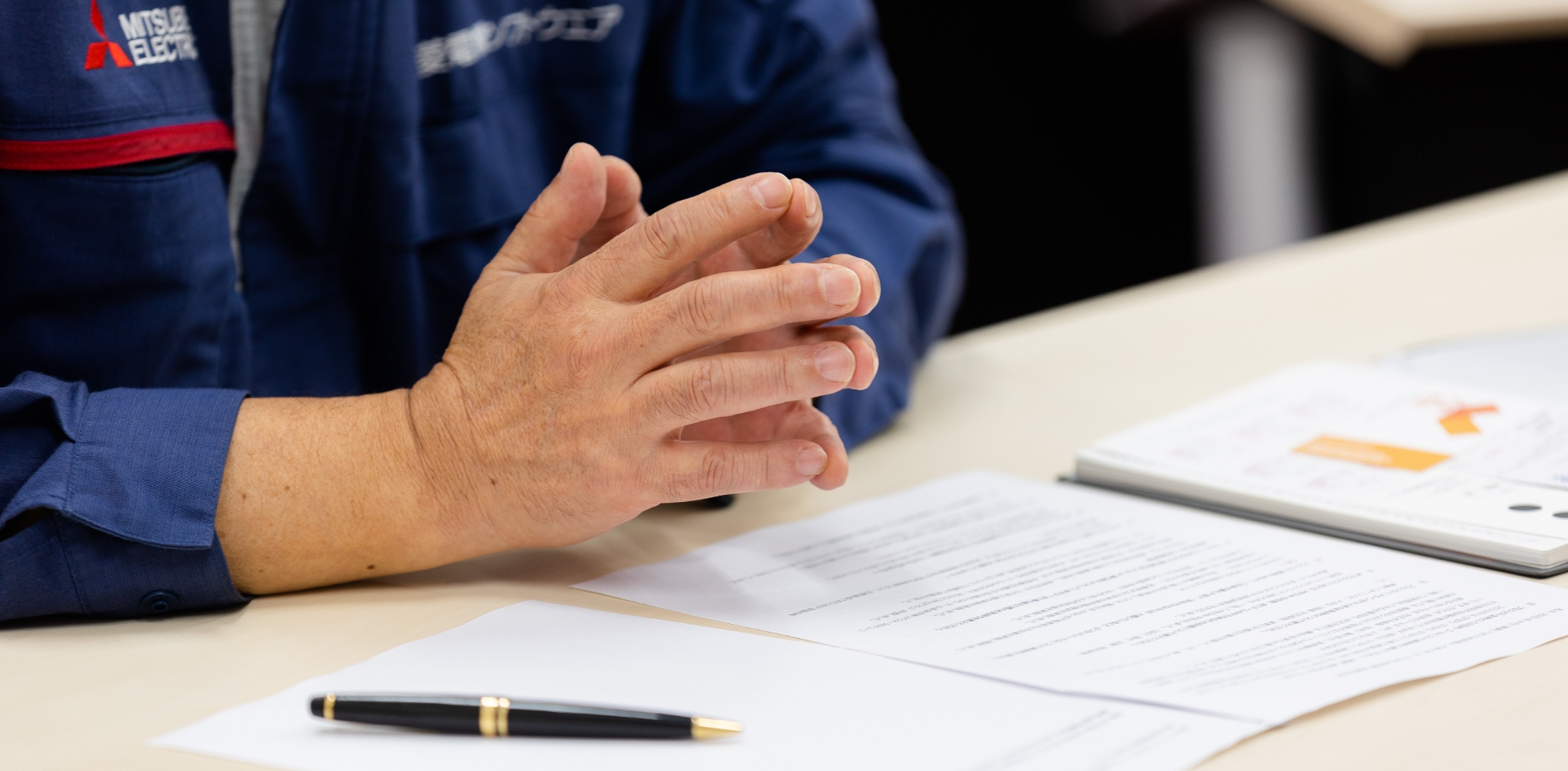
─開発に際して苦労された点は何でしたか。
- T.S:
- 正式受注となって、プロジェクトにN.Tさんが加わってくれました。
- N.T:
- “満を持してのN.T投入”です(笑)。
- T.S:
- 開発者としてどのような思いでしたか。
- N.T:
- 大規模プロジェクトなので責任の重さは感じましたが、それ以上に「やってやろう!」とワクワクする思いの方が大きかったですね。とはいえ、もちろん不安もありました。その一つがお客様とのコミュニケーションです。どの企業にも社内の共通言語や暗黙の了解といったものがあり、プロジェクトの動き出しには苦労するものです。例えば「マスク」という単語一つとっても、企業によってその意味が違います。ささいなことでも理解が十分でないままにプロジェクトを進めていくと、大きな行き違いにつながりかねません。このプロジェクトでは毎週お客様とのミーティングを行い、互いの認識に齟齬がないか、溝を埋めていきました。リモートではなく、対面での打ち合わせにこだわったのもそのためでした。
- T.S:
- 私はプロジェクト責任者(当時)として、毎月一回進捗状況を事業所長経由で本社に報告する役目を担いました。プレッシャーではありましたが、それだけ社内でも期待されている大型プロジェクトだと感じ、何としても成功させなくてはとの思いを強くしましたね。
- N.T:
- 実際の開発において大きなハードルとなったのが、OPCサーバとPLC(シーケンサ)の間の通信でした。膨大な信号量に対して期待される通信速度性能を発揮できるのか、ここがこのプロジェクト最大のボトルネックになるだろうと考えていました。当初の性能調査においては、期待した速度には遠く及ばない結果となったのです。
- T.S:
- 当初想定していた通信速度に対し、8倍もの時間がかかることが判明しました。あまりのことに「これじゃ使い物にならないよ!」と叫んだのを覚えています。ツール本体のチューニングによって通信時間を半減できましたが、これでもまだお客様に提供できる性能は実現できませんでした。
- N.T:
- 半導体製造に使用される何十種類ものガスの濃度など、大量のデータをやりとりするため、通信に非常に大きな負荷がかかってしまったためです。チューニングを進めながら大量の仮想データを流し込んでテストを繰り返しました。最終的にはデータの構成そのものを表示と蓄積で分けるなど、今回のシステムに合うように再構成し、なんとか当初の想定通り一秒にまで短縮できました。
- T.S:
- その結果を聞いて、プロジェクトの大きな山を越えたとホッとしたことを覚えています。案件を受注した際、開発メンバーとしてN.Tさんに声をかけて本当によかったです。
- N.T:
- 正解だったでしょう?(笑)実は、T.Sさんと私は地元の中学で同級生だったんですが、直接仕事をしたことはなかったんですよね。
- T.S:
- このプロジェクトでようやくご一緒できて、嬉しかったです。さまざまなハードルもN.Tさんがいてくれたから乗り越えられたと思っています。
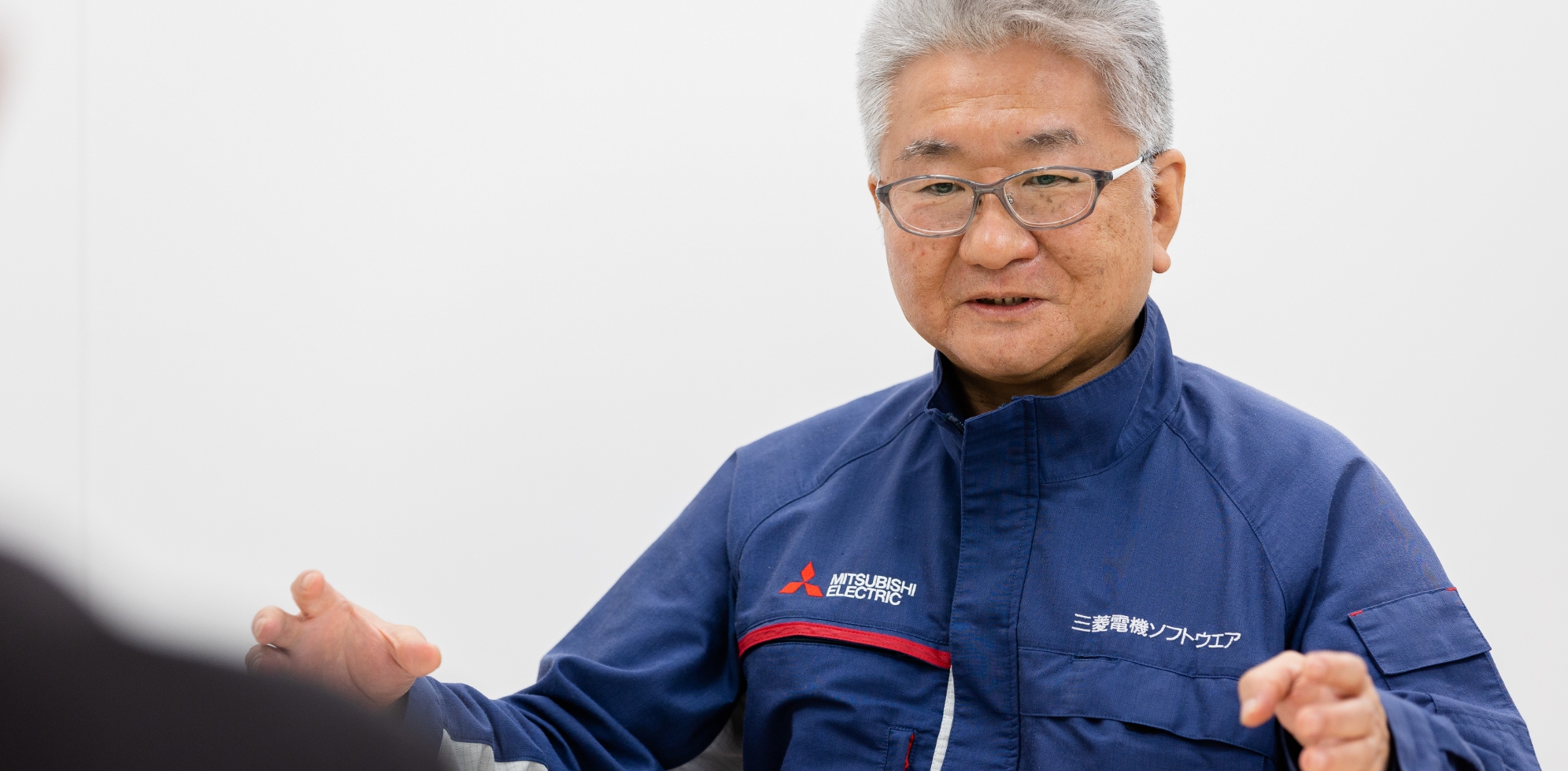
─プロジェクトはまだ進行中とのことですが、達成感などはありましたか。
- N.T:
- 新しい半導体工場は三期に分けて工事が進められており、全体のゴールは数年後の予定です。これからもプロジェクトは続くので、やりきった実感はまだないですね。
- T.S:
- それでも期ごとに生産ラインが完成するたび、『GENESIS64™』を組み込んだ監視システムを導入するので、その都度達成感は得られます。
- N.T:
- そうですね。サーバを入れてPLC(シーケンサ)と機器をつなぎ、通信も問題なく行われ、画面にちゃんと表示される瞬間はいつもドキドキします。無事に「完了」と表示されるとホッとします。もちろんうまくいって当たり前なんですが、何度やっても絶対大丈夫という保証はありません。いつも緊張しながら取り組んでいます。
- T.S:
- 実際に半導体工場で産業用ガスが使用されるシーンを見ることができたら、また違った手応えを感じるのでしょうが、セキュリティ面などが厳重に管理されているため私たちが足を踏み入れることはできません。だからこそ常にユーザーのことをリアルにイメージし、使い勝手に配慮したシステムを実現するよう、心がけています。
- N.T:
- 私自身は今回のプロジェクトを通じて、実装前の課題解決の“思考の時間”を十分に取れたことがやりがいにつながりました。当社に限らず、現代ではあらゆる場面でモノづくりにかける時間が短くなってきていると感じます。お客様からは迅速な開発を求められますし、技術の進歩が急速なのも背景にあります。しかし今回のプロジェクトでは、たっぷりと時間をかけて考えることができました。途中で作業の手を休める時間は、一見すると無駄に思えますが、実は思考を整理し、新たなアイデアを生むことにもつながるんです。エンジニアとしてこうした“思考の時間”を持てたことが、一番嬉しかったです。
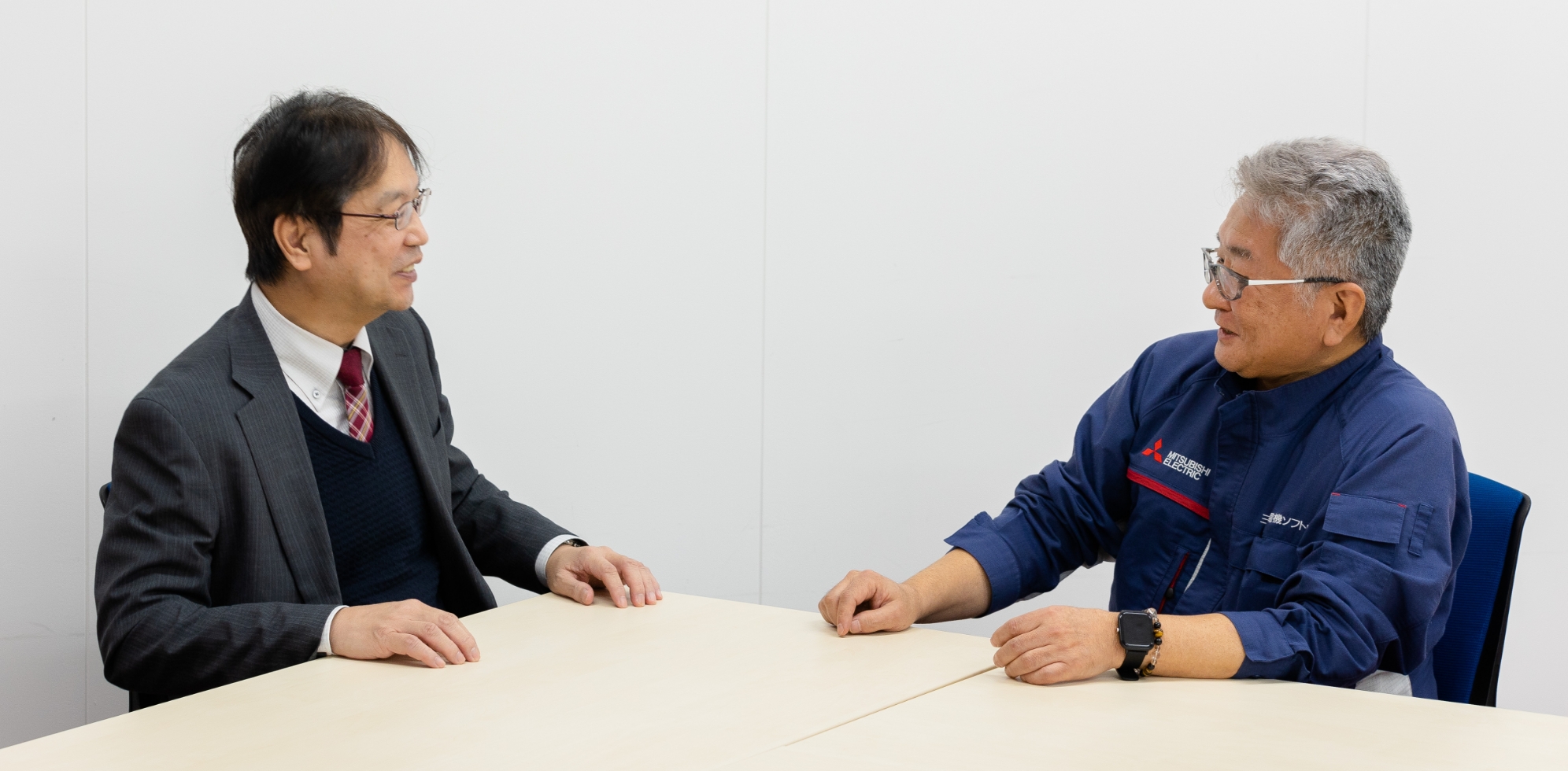
―今回のプロジェクトの価値と今後の展望についてお聞かせください。
- T.S:
- 社会への提供価値という点では、半導体製造工場新設に携わったことで半導体の安定供給に貢献できたと自負しています。家電や車、スマートフォンをはじめ、半導体は生活に必要なあらゆるものに使われており、「産業の米」とも呼ばれています。最近では急激な需要増に供給が追いつかず、生産現場は深刻な影響を受けています。そうした中、ガス供給監視システムの開発を通じて新しい工場の立ち上げに参画できたことは、日本のモノづくりを縁の下の力持ちとして支えられたのではないでしょうか。
- N.T:
- 学生の皆さんが使っているスマートフォンのカメラセンサーも、今回のプロジェクトを通じて生産されたものかもしれませんね。
- T.S:
- さらに嬉しいのは、このプロジェクトをきっかけに既に他社の大型工場新設にまつわるご相談をいただいていることです。また中小規模の工場も含めて既にSCADAを導入している工場では、『GENESIS64™』へのリプレースへのご相談をいただいています。さらに産業用ガスメーカー様からはカーボンニュートラルに向けた新製品に『GENESIS64™』を搭載したいとのご相談もいただいており、今後の展開が楽しみです。当社にとっての市場拡大にも貢献していきたいですね。
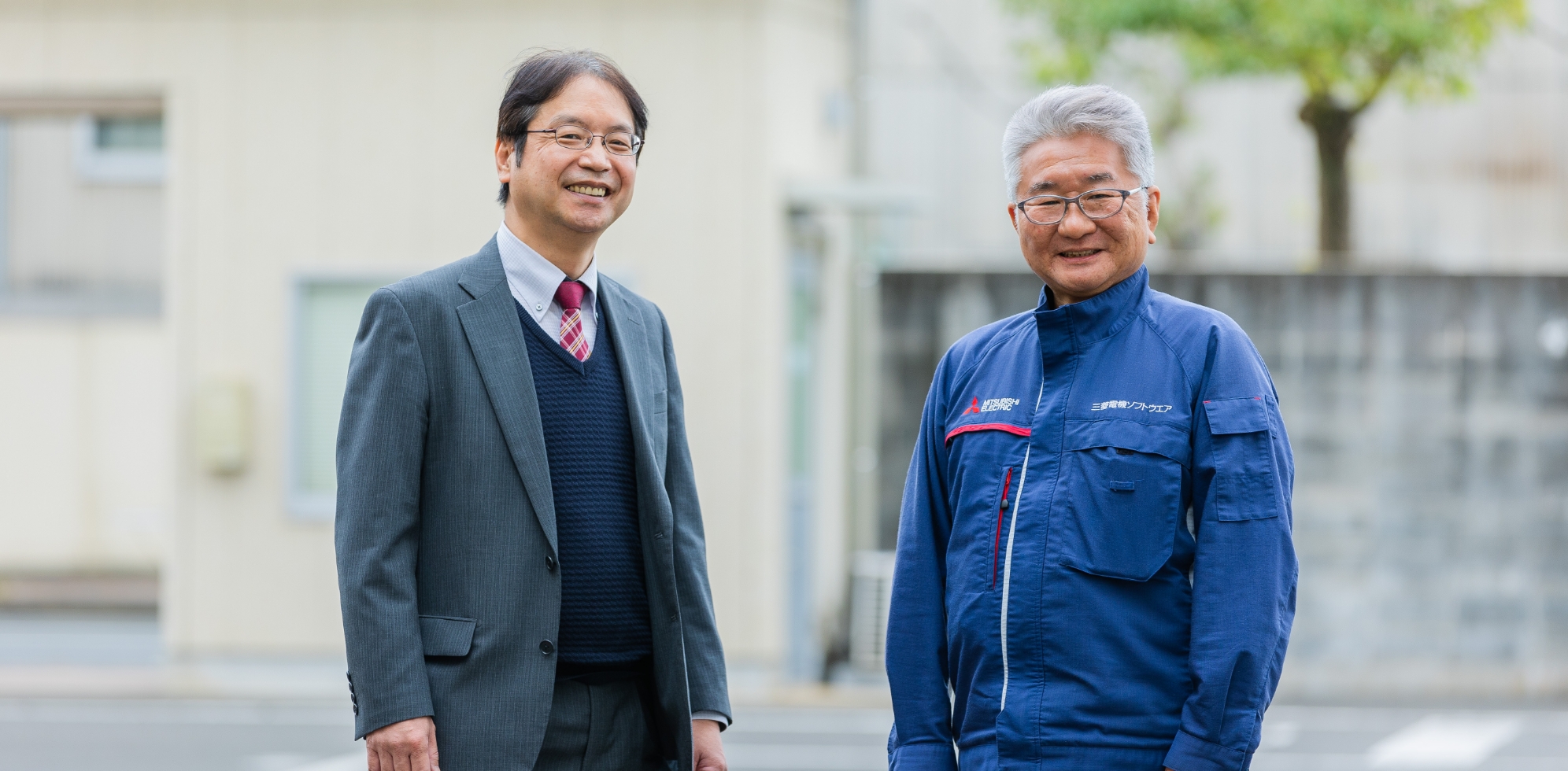
RECOMMENDED CONTENTS