未来を拓くための技術PROJECT STORY_02
ワイヤ・レーザ金属3Dプリンタ開発プロジェクト
省資源、省エネ、自由なモノづくりを実現する
ワイヤ・レーザ金属3Dプリンタの開発。
PROLOGUE
ワイヤ・レーザ金属3Dプリンタ開発プロジェクト
CO2排出削減や資源の有効活用などが社会的課題となる中、金属3Dプリンタは設計データを直接プリントして製品を製造できるため、従来の切削工法に比べ省資源、省エネで金属製品を製造でき、モノづくりのデジタル化につながる手法として期待を集めている。しかし、現在主流の金属粉末を材料とする3Dプリンタは、材料コストなどで課題があり、幅広い産業で利用できるわけではない。今回、三菱電機ソフトウエアが挑んだのは、それらの課題を解決するワイヤ・レーザ金属3Dプリンタ(三菱電機製品)のソフトウェア開発だ。世界初(※)となる技術も盛り込まれたその製品開発は、前例のない中での挑戦となった。まさに手探りで道を切り拓くようなこの一大プロジェクトに、一体どのような想いで挑んでいったのか。
(※)2022年2月24日現在。三菱電機(株)調べ
MEMBER
-
プロジェクトリーダー
H.I
名古屋事業所 加工機システム開発部
2016年入社
情報システム学研究科 情報メディアシステム学専攻卒 -
システムエンジニア
K.M
名古屋事業所 加工機システム開発部
2019年入社
工学研究科 情報工学専攻卒
STORY
─早速ですが、本プロジェクトの概要をお伺いできますか。
- H.I:
- 今回、私たちが取り組んだのは、これまでにない新しい加工方式の金属3Dプリンタに搭載されるソフトウェアの開発です。従来の金属3Dプリンタの多くは、微細な粉末金属をレーザなどで溶かして固めた層を積み重ねていく方式をとっています。しかし、この方法は加工に時間がかかってしまう、粉末の一部が加工に使われず無駄になる、内部に空孔が多くできてしまうなどの問題点を抱えていました。
- K.M:
- これらに対応するために生まれたのが「ワイヤ・レーザDED方式」という新たな方法を採用した金属3Dプリンタです。これは金属ワイヤを直接加工部分に供給し、それをレーザで溶かして固めることで造形していく方式です。従来に比べて加工時間を短縮でき、材料の無駄がほとんどなく、空孔の少ない緻密な造形が可能になります。
- H.I:
- また、加工性能だけでなく、社会的課題への貢献という観点でも「ワイヤ・レーザDED方式」には大きなメリットがあります。より低コストで空孔のない造形を実現することで、さまざまな産業分野における3Dプリンタ利用が拡大し、CO2排出削減と資源の有効活用に寄与することができるのです。
- K.M:
- さらに、3Dプリンタは多品種少量生産に向いているため、この方式を普及させることで、さまざまな人々のニーズに応えて多様な製品がつくられる豊かな社会の実現を本プロジェクトは目指しています。
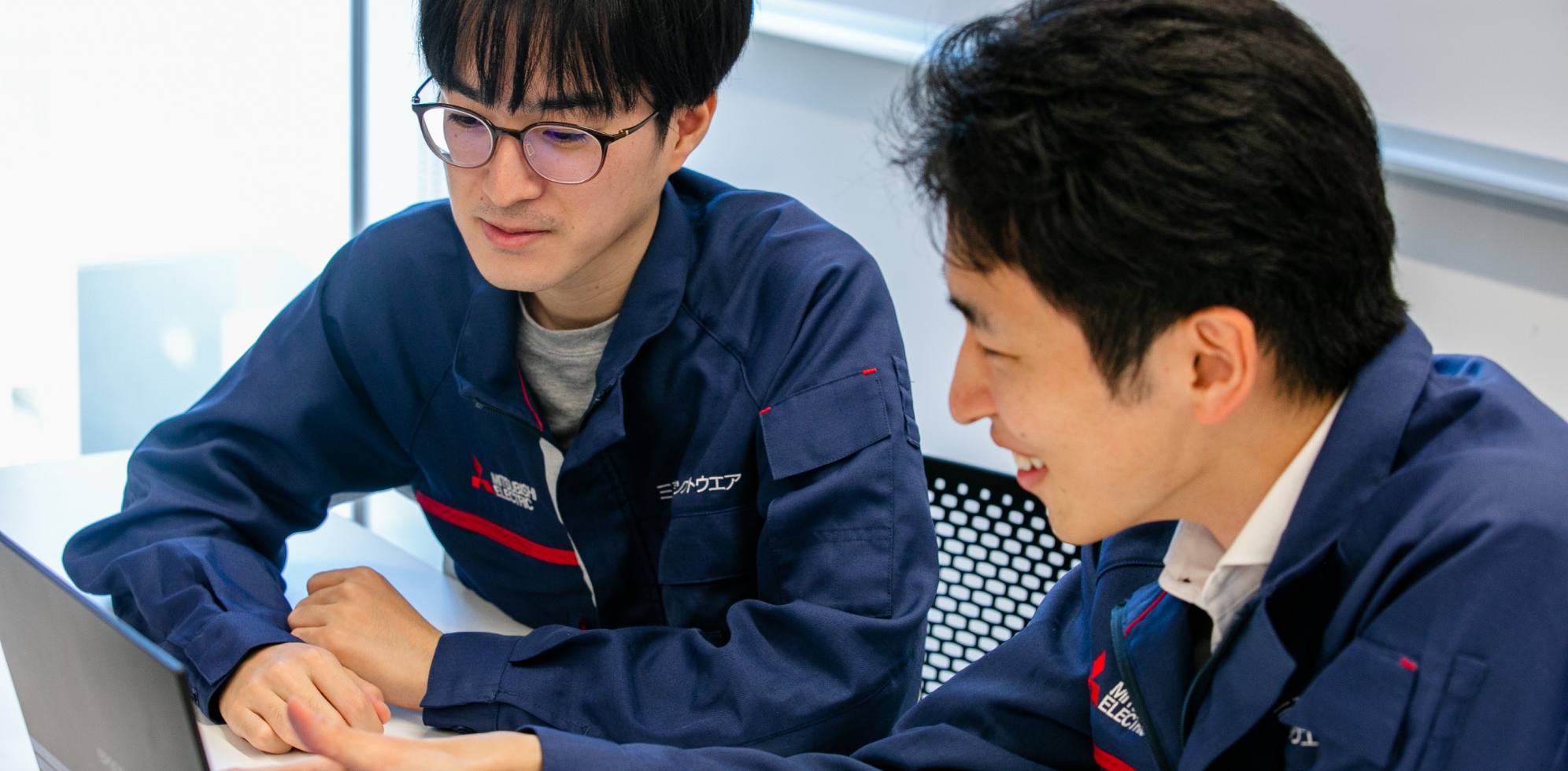
─どのような経緯で、このプロジェクトに参加することになったのでしょうか。
- H.I:
- 2017年にお客様の三菱電機(株)に声をかけていただく形で始まりました。お客様では、このプロジェクト始動の数年前から3Dプリンタで金属の造形を行う研究に着手していて、具体的に製品化するタイミングで依頼いただいたのがスタートです。当社が担当したのは、UI画面と制御に関するソフトウェア開発です。画面開発チームでは、3Dプリンタの状態や制御ソフトウェアの機能をわかりやすくユーザに提示し、直感的に操作できるUI画面の設計や開発を担当。そして、私とK.Mさんは制御ソフトウェア開発チームとして、レーザ出力、ワイヤ送給、加工ヘッドの移動指令をどのように協調動作させるかという3Dプリンタの造形能力に直接関わる部分を設計・開発しました。
- K.M:
- プロジェクト開始当時、私はまだ入社していなかったのですが、これまで先輩方が築き上げてきた信頼と実績のおかげもあり、「工作機械のソフトウェアを作るなら三菱電機ソフトウエアしかいない」と迷いなく指名してもらったと聞いています。
- H.I:
- その信頼は嬉しかったですが、その分責任の重さも感じました。会社を代表して、その信頼に応えていかなければと身の引き締まる思いでした。それに当社としても、ご依頼いただいた三菱電機(株)の名古屋製作所としても、まったく新しい工作機械の製品開発は久しぶりの試みだったため、期待と責任の大きさをひしひしと感じていました。
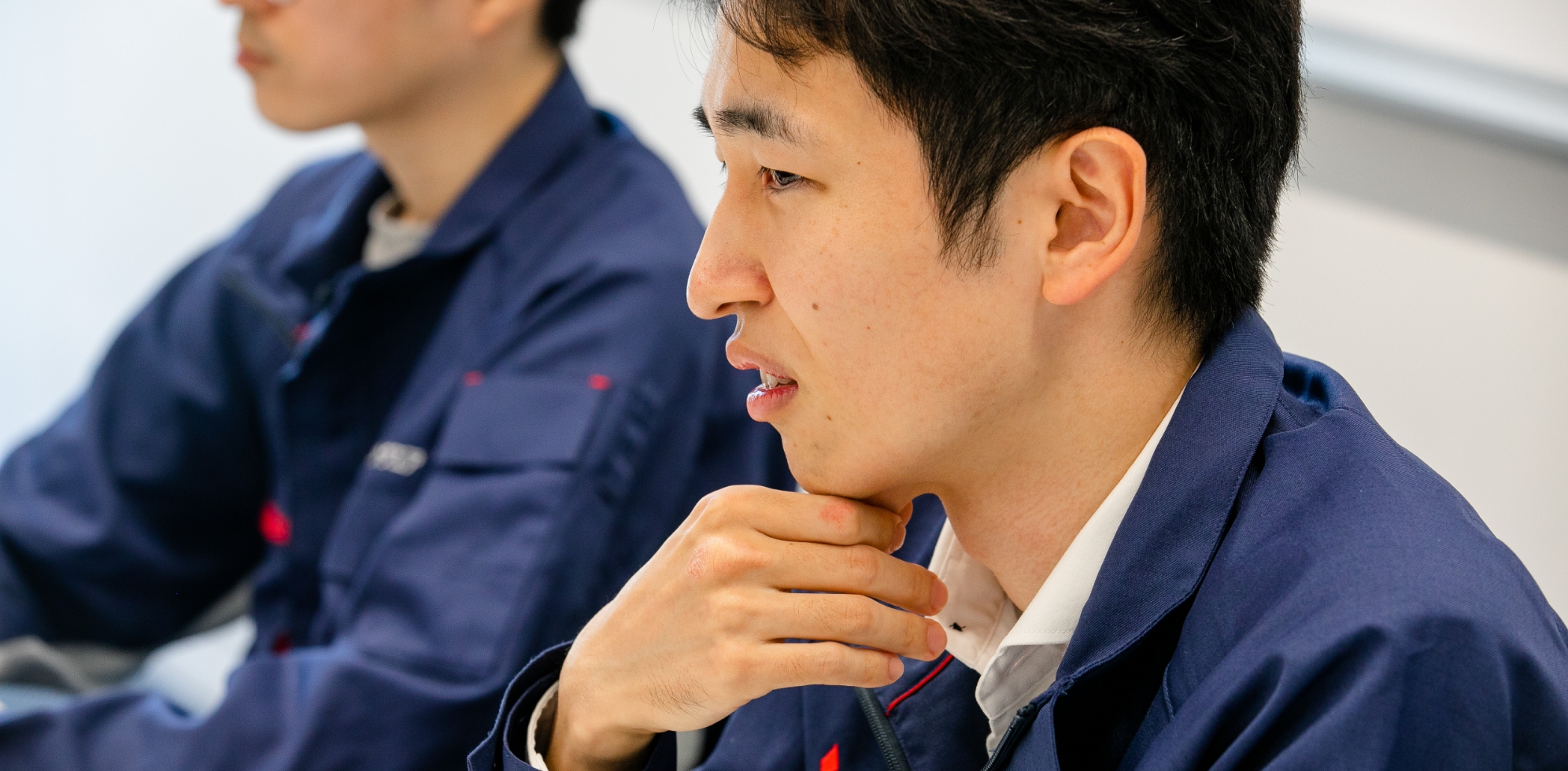
─大きな期待のかかる一大プロジェクトですが、幸先よくスタートは切れたのでしょうか。
- H.I:
- 正直なところ、最初はそこまで苦戦しないのではと考えていました。なぜかといえば、製品自体は新しいものですが、構成する技術要素の一つひとつは、これまで開発を積み重ねてきた実績があり、私たちの強みとする技術だったからです。
- K.M:
- 当社の担当したソフトウェア領域で今回必要となる技術は大きく3つ。加工ヘッド部分の位置制御、ワイヤ供給の制御、そしてレーザの制御です。これらの技術は、ワイヤ放電加工機やレーザ加工機といった既存の工作機械向けに当社が開発を積み重ねてきた技術で、この3つをすべて持っているのは当社ならではの強みなのです。
- H.I:
- そのため、当社が持つ技術をどう組み合わせるかに注力することがポイントなのですが、これがそう簡単な話ではありませんでした。例えば、同じ制御内容でも、ソフトウェアによる実現方法にはさまざまなアプローチがあり、どの方法がこの製品に最適か意見の分かれる場面も多く、合意形成するのも一筋縄ではいきませんでした。
- K.M:
- お客様、当社ともにさまざまな工作機械の開発メンバーが集まって発足したチームで、新製品開発を進めていくのは、いろいろな面で認識のすり合わせなど、苦労も多かったのではないかと思います。
- H.I:
- たしかにすべてスムーズとはいきませんでしたが、お客様の担当者もソフトウェアの知見がある方だったので、一つひとつソフトウェアの実現方法を図面に起こしながら「この部分はこうした方がシンプルに構成できますよね」と議論を交わし、自然と認識が揃っていきました。要求事項と既存のソフトウェア構造をきちんと整理して図式化すれば、おのずと正解が見えてくるものなんだなと感じました。
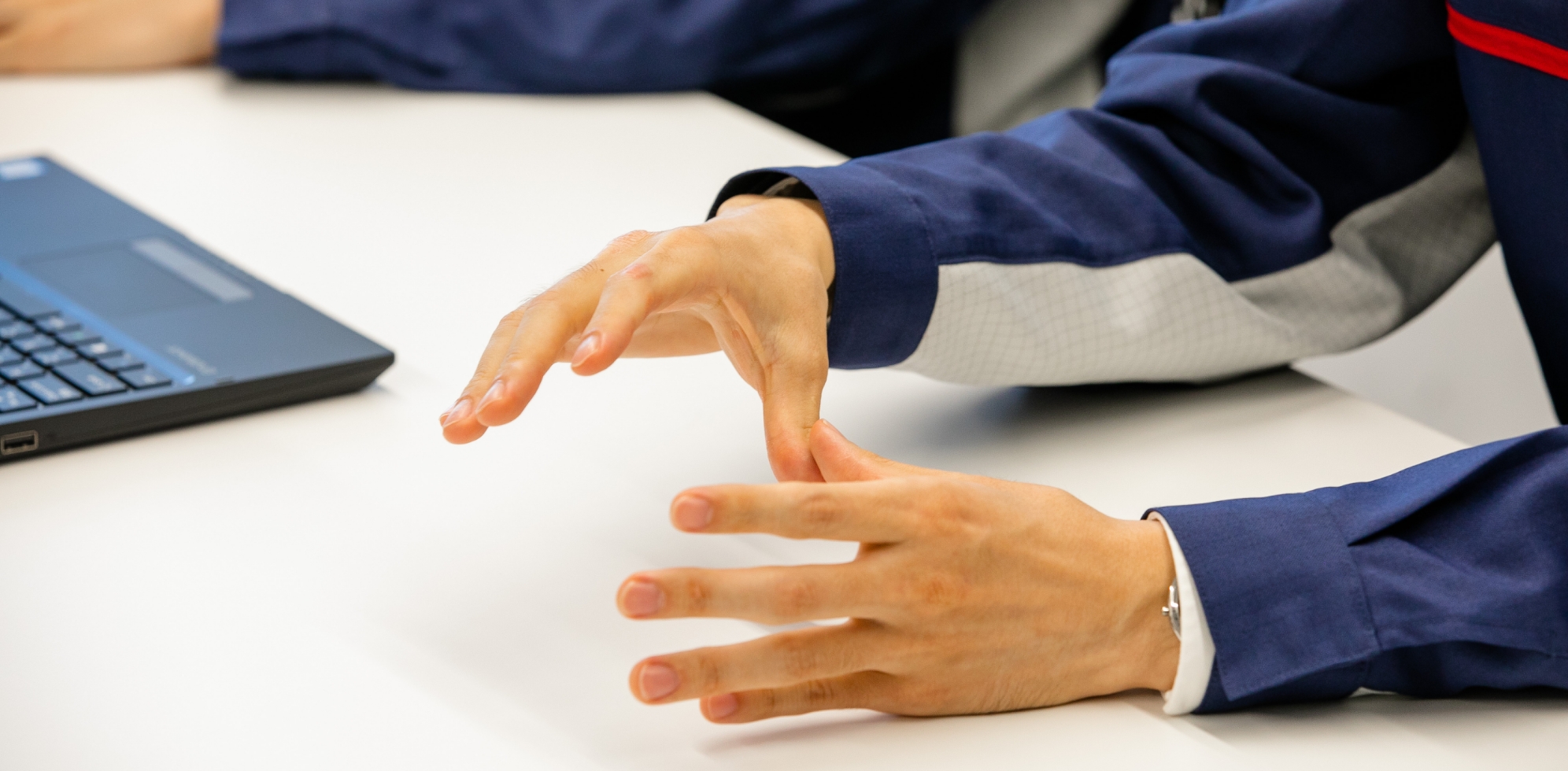
─技術的な面で難しかった部分もお伺いできますか。
- H.I:
- 多くありましたが、わかりやすい例を挙げると、加工開始と終了部分の制御です。加工ヘッドとワイヤ送給の速度が目標速度に達して等速で運動しているときは、造形も比較的安定します。一方、その安定状態に達するまでの過程では加工ヘッド速度、ワイヤ供給量、そしてレーザ出力の3つを適切な関係に保ったまま協調して加減速する必要があり、技術的に苦労しました。ですが、造形実験を繰り返して少しずつ改善していきました。
- K.M:
- 当時の実験画像を見せてもらったところ、一直線を積み重ねて壁を造形するだけの実験でも、層を重ねると上の方の層が歪んでしまっていたのを覚えています。まっすぐの壁すら造形できないのに、複雑な3D加工ができるようになるのかと不安になったことを覚えています。
- H.I:
- K.Mさんが本プロジェクトに参加したのは、ちょうどこの課題にトライしている時期でした。プレッシャーも大きかったと思いますが、メンバーに加わってくれて私としてはとても助かりましたし本当に感謝しています。
- K.M:
- 確かにプレッシャーはありましたが、同時にやりがいも感じていました。初めて任せてもらった仕事は、レーザ射出のタイミング調整で、1000分の1秒単位で調整するものでした。当然、目で見てもズレなどわからず、実験後にログデータを解析してようやくわかるレベルの誤差。ここまで精密な制御が必要なのか、それが新人の自分にできるのかと日々試行錯誤しながらも、先輩のサポートもあって何とかやり遂げられました。
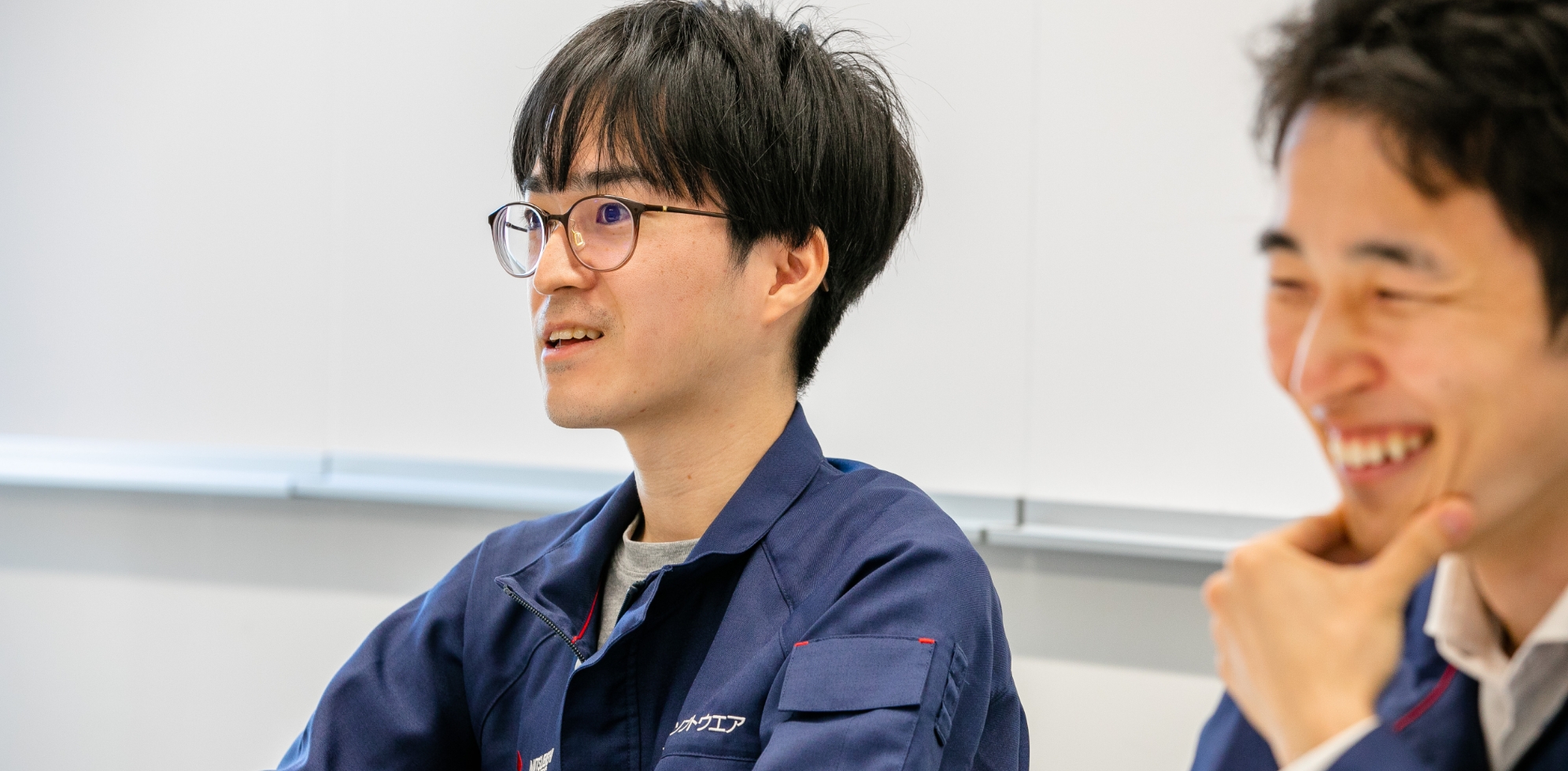
─そこからはどのように開発が進んでいったのでしょうか。
- H.I:
- 単純な壁のような形状は安定して造形できるようになったので、より複雑なベンチマーク形状の造形にトライするサイクルに入りました。新しいベンチマーク形状の造形にトライするたびに新たな課題点が見つかったため、加工ヘッド位置、ワイヤ供給、レーザ出力の協調制御をブラッシュアップして対応しました。加工性能は順調に向上していきましたが、スムーズに開発が進んだというには取り組む課題が少々多かったですね。この実験と改良の積み重ねに2年近くかかりましたから。
- K.M:
- 期間としては長かったですが、個人的にはやりがいも大きかったです。特に、自分が修正作業をした箇所について、すぐに実機での実験結果のフィードバックがもらえるのはありがたかったです。上手くいったのがわかれば嬉しいですし、上手くいかなくても「じゃあどうしようか」とすぐに考えてまた実験できる。これは新製品開発のプロジェクトならではの醍醐味ではないでしょうか。
- H.I:
- そうした実験を積み重ねて、目標としていたベンチマーク形状の加工が成功したときは「やっとここまで来たか……」と技術者として感慨深かったです。4年近くかけて辿り着いた時のあの気持ちは、このプロジェクトだからこそ味わえたものだと思います。
- K.M:
- ただ、加工性能が目標に達しても、まだ終わりではないのです。実験装置ではなく、製品として販売することが目的なので、加工精度以外の観点でもさまざまな機能が必要になります。例えば、安全性の確保は大きなポイントです。特に今回はレーザを使用するため、通常の工作機械にはない特別な配慮も必要でした。
- H.I:
- レーザが漏れれば失明や火傷もあり得ますし、使用しているモータも大きいため、手が挟まれば大事故になります。こうしたトラブルが絶対に起きないよう、機械の不備を察知して加工を停止させる機能など、作業者の安全を守るための制御プログラムを実装していきました。
- K.M:
- 安全面も含め、あらゆる観点から製品としての認可が降りたのが、2022年2月の現品会議。発売開始が2022年3月なので、本当に発売する直前まで調整していました。
- H.I:
- その分、無事発売された時の達成感も大きかったです。発売から少し経つと、プレスリリースや展示会の反響なども耳に入るようになり、自分のやってきたことが世に出たんだと実感が湧いてきましたね。
─無事に製品も発売された今、次に目指す目標をお伺いできますか。
- H.I:
- やはり、性能をさらに向上させていきたい想いはあります。特に、加工速度を上げていきたいです。今回の金属3Dプリンタは、従来の工作機械に比べて短時間で部品を製造できることがアピールポイントの一つであり、工作機械において加工時間は生産性に直結しているため、利用されるお客様の売り上げを左右する要素でもあります。加工速度を上げることで、さらにお客様のビジネスに貢献できる。そんな3Dプリンタへと改良していきたいです。
- K.M:
- 私も、同じく性能向上に取り組み続けたいです。もう少し時間が経つと、製品を購入したお客様からフィードバックが得られると思います。さまざまな実験を繰り返して自信を持って世に出した製品ですが、実際の現場で想定通りの精度や速度が出せているか。お客様のニーズに応えきれているか。生の声を拾い上げて、製品に反映させるのが次の目標です。
- H.I:
- お客様の声を反映させながら製品を磨き上げ、普及を進めていきたいと考えています。その結果、設計から生産までのリードタイムや立ち上げコストも低下し、多品種少量生産のハードルが下がるはず。本製品を通じて、より多様なニーズに対応した多様な製品が生産される豊かな社会を実現できればと思っています。
- K.M:
- また、3Dプリンタを活用してモノづくりをデジタル化することは、製造現場における労働力不足や職人技の継承者不足の解決にも寄与します。様々な製造現場で使って頂けるように、改良を重ねて本製品を育てていきたいです。従来手作業だった溶接工程を金属3Dプリンタに置き換え、自動化、デジタル化するという話も出ています。
- H.I:
- 製品を通じたお客様や社会への貢献に加え、新しい技術や製品を生み出していく文化を今以上に社内に根付かせていくことも目標です。私たちの一番の武器であり、資産となるのは技術。だからこそ、常に新しい技術を取り入れ続けることが重要です。その意味で、レーザとワイヤと同時5軸の協調制御という世界初(※)の技術を確立できたことは、一つのロールモデルになり得るはずです。このプロジェクトを一つのきっかけとして、三菱電機ソフトウエアをもっともっと進化させていきたいと考えています。
(※)2022年2月24日現在。三菱電機(株)調べ
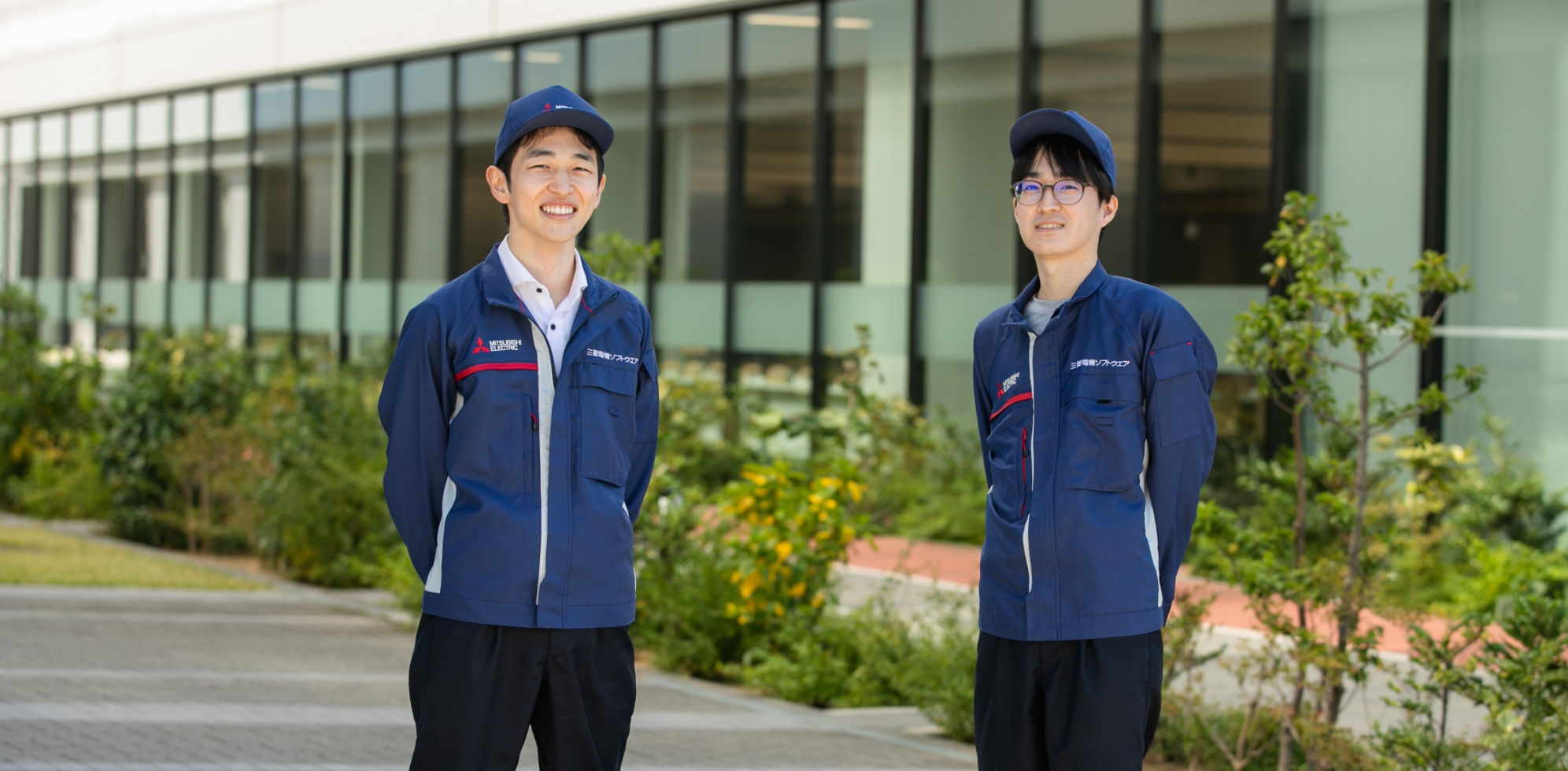
RECOMMENDED CONTENTS