テクノロジー
技術レポート:アーカイブ
Category:FAソフトウェア開発
MITSUBISHI CNCにおける振動切削機能の開発
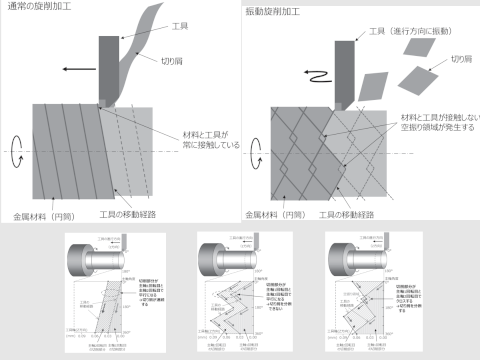
製造現場は生産性の向上が常に求められている。一方、工場内の設備や装置を構成する機器が多様化しており、装置の高機能化・複雑さが増している。そのため、設備や装置で異常が発生する金属加工のうち、円筒の金属材料を回転させながら工具を動かして削っていく旋削加工において、切削時に生じる切り屑はリンゴの皮むきの様に細長く連続した形になり、材料や工具に絡まりやすくなる。絡まった切り屑を放置すると不良ワークや工具の損傷につながるため一度加工を止めて切り屑を取り除く必要があった。この問題を解決するため、工具に低周波の振動を与えることで加工時に生じる切り屑を細かく分断することを可能とする振動切削加工制御を三菱電機(株)と協力して開発した(特許8件出願)。振動切削加工制御は、金属材料を掴んでいる主軸の回転に同期するよう、工具側のサーボ軸を振動制御することで、図の様に材料と工具が接触しない空振り領域を発生させ、切り屑の分断を可能にしている。切り屑が細かく分断されることで下記のメリットが生じる。
・切り屑が材料や工具に絡まなくなり、不良ワークの発生や工具の破損が減少する。
・材料や工具に絡まった切り屑除去のために加工を止める回数が減少し、生産性が向上する。
・切り屑の受箱が堆積しても嵩張らないため、掃除する頻度が減り、作業効率が向上する。
・切削抵抗が減少するため、チタンやステンレスなど硬い材料の加工にも適する。
本稿では、この三菱CNC装置に搭載した振動切削加工制御機能を開発した際の課題とその対応を紹介する。
参考情報:
- この技術レポートは、当社が展開するFA・産業メカトロニクス事業のFAソフトウェア開発ソリューションに係る技術について著述されたものです。
- FAソフトウェア開発ソリューションは、名古屋事業所が提供しています。
MITSUBISHI CNC における振動切削機能の開発 名古屋事業所 モーション・ドライブシステム統括部 NC コア開発部 NC 応用開発課 ・岩田 好史・冨田 圭祐・川西 昂弥 要 旨 金属加工のうち,円筒の金属材料を回転させながら工具を動かして削っていく旋削加工において,切削時に生じる切り屑はリンゴの皮むきの様に細長く連続した形になり,材料や工具に絡まりやすくなる。絡まった切り屑を放置すると不良ワークや工具の損傷につながるため一度加工を止めて切り屑を取り除く必要があった。この問題を解決するため,工具に低周波の振動を与えることで加工時に生じる切り屑を細かく分断することを可能とする振動切削加工制御を三菱電機(株)と協力して開発した(特許8件出願)。振動切削加工制御は,金属材料を掴んでいる主軸の回転に同期するよう,工具側のサーボ軸を振動制御することで,図の様に材料と工具が接触しない空振り領域を発生させ,切り屑の分断を可能にしている。切り屑が細かく分断されることで下記のメリットが生じる。・切り屑が材料や工具に絡まなくなり,不良ワークの発生や工具の破損が減少する。・材料や工具に絡まった切り屑除去のために加工を止める回数が減少し,生産性が向上する。・切り屑の受箱が堆積しても嵩張らないため,掃除する頻度が減り,作業効率が向上する。・切削抵抗が減少するため,チタンやステンレスなど硬い材料の加工にも適する。本稿では,この三菱CNC 装置に搭載した振動切削加工制御機能を開発した際の課題とその対応を紹介する。9 1.まえがき 旋削加工において工具を振動させて切り屑を分断する技術自体は1960 年代には考案されており,工作機械にカムを用いた特殊な振動発生機構を取り付けるなどして実現されていた。しかし,加工ワークに合わせた調整が必要であり,また機械コスト増などの理由により広く普及するには至らなかった。振動切削加工制御では,CNC で振動を制御することで特殊な振動発生機構を不要とし,ワークに合わせた調整なしでテーパや円弧,穴あけ,ねじ切りなどさまざまな加工に対応可能となる。本稿では振動切削加工制御ソフトウェアの開発課題とその対応について紹介する。2.振動切削加工制御の仕組み2.1 振動切削加工制御概要円筒の金属材料を回転させながら工具を動かして削っていく従来の旋削加工では,図1に示すように工具は進行方向へ一定速度で移動する。そのため切削時に生じる切り屑は細長く連続した形になり,材料や工具に絡まりやすくなる。図1.従来の旋削加工振動切削加工制御では,工具を動かす工具軸(Z 方向)を制御して微小な前進/後退指令を繰り返すことで工具の進行方向に低周波の振動を生成する。生成する振動の周波数は主軸1回転当たりの振動数を指定することで決定する。図2−1に振動数を2.0 とするケース,図2−2に振動数を1.5 とするケースを示す。図2−1.主軸1回転当たりの振動数が2.0 の場合図2−2.主軸1回転当たりの振動数が1.5 の場合振動数を2.0 とする場合,図2−1に示すように切削部分が主軸1回転目と主軸2回転目で平行となり,材料10と工具が常に接触するため切り屑を分断できない。それに対して振動数を1.5 とする場合,図2−2に示すように主軸1回転目と主軸2回転目の切削部分がクロスすることで材料と工具が接触しない空振り領域が発生し,切り屑の分断が可能となる。このように振動切削加工制御は主軸1回転当たりの振動数に,0.5 回転の端数(0.5/1.5/2.5/3.5・・・)を持たせ,主軸の回転に同期して工具を振動させる。2.2 切削開始時の振動制御図3に示すように,切削開始位置から指令した振動幅で振動を開始すると工具移動方向の切り込み量が大きくなり加工面が荒くなる。また工具の温度が上がり工具寿命にも悪影響がある。振動後退時には工具がワークに干渉し,工具を破損する危険がある。そこで切削開始時は図4に示すように徐々に加速する工具が進んだ分だけ後退することで振動も徐々に大きくなる制御とした。これにより切削開始時の切り込み量が大きくなりすぎることを防ぎ,後退時のワークへの干渉問題も解決した。図3.切削開始時の振動問題点図4.切削開始時の工具軸(Z 方向)位置2.3 主軸と工具軸(Z 方向)の同期を保持する振動切削加工制御では金属材料を掴んでいる主軸の回転に,工具を動かす工具軸(Z 方向)が同期して振動することで切り屑の分断が可能となる。そのため,切削中に工具の送り速度が変化しても同期を保ち,かつ図2−2に示す空振り領域を発生させるために速度変化に合わせて振動幅を変化させる必要があった。図5−1,図5−2に示すように速度変化点の前後で,主軸1回転当たりの工具軸(Z 方向)1.5 振動を保持する。図5−1は振動幅が速度変化点の前後で同じ場合(振動A)で,速度変化点後,空振り領域ができないため切り屑を分断できない。図5−1.速度変化と振動幅(振動幅が同じ)図5−2は振動幅が速度変化点の前後で変化する場合(振動A <振動B)で,振動幅が速度変化点の前後で工具軸(Z 方向)の速度が大きくなる変化に合わせて,空振り領域ができるように振動幅を大きくする。図5−2.速度変化と振動幅(振動幅が変化)このように,加工プログラムの速度指令やオーバライドにより切削中の送り速度が変化する場合,切り屑を分断するために,速度に合わせて振動幅を変化するように制御した。113.用途の拡張3.1 ねじ切り加工への対応ねじ切り加工においても,加工時に生じる切り屑の問題は発生する。しかし,図6に示すように従来の振動切削加工制御(工具の進行方向に振動させる方法)では,ねじ溝を潰してしまう。図6.ねじ切り加工における振動切削加工制御の課題そこで,ねじ切り専用の振動切削加工制御を開発した。図7に示すようにねじ切り加工では複数回の切り込みによってねじ溝を掘る点に着目し,図8に示すように進行方向に対し垂直方向(X 方向)に工具を振動させ,且つ切り込みごとに振動の位相を180°ずらした。これにより図9に示すように偶数回と奇数回の切り込みで工具の移動経路が交差するようになり,材料と工具が接触しない空振り領域が発生して切り屑の分断が可能となった。また図10 に示すように切り込み量から振動幅を自動計算することで,空振り領域が必ず発生するよう制御した。図7.ねじ切り加工の切り込み図8.ねじ切り加工専用の振動切削制御図9.ねじ切り加工における切り屑の分断図10.ねじ切り加工における振動幅の調整最後の切り込み(図7の例では4回目の切り込み)は,振動しないことで,切り屑の分断を行いながら,削り残し部分の加工を行う。124.機械特性に対応する4.1 機械固有の周波数特性に対応する振動切削加工制御を適用する工作機械において,特定の周波数帯で振動制御を行うと機械との共振が発生し,機械のねじが緩むなどの問題が起こる。そこで,あらかじめ工具軸(Z 方向)ごとの共振周波数帯をパラメータとして設定することで,振動切削加工制御においてその周波数帯での振動制御を行わないようにした。4.2 機械のイナーシャ(慣性)に対応する振動切削加工制御を適用する工作機械において,イナーシャによる工具軸(Z 方向)の追従遅れが原因でユーザの指定した振動幅とならず,切り屑が分断されないケースがある。そこで,図11 に示す振動特性(指定振動幅に対するフィードバック振動幅)データを元に,指定振動幅を補正する制御を開発した。図11.振動特性データ振動特性は振動幅と周波数,工具軸の速度ループゲインに依存する。また,加工評価から振動特性は非切削加工と実加工で差異がでるが,非切削加工の振動特性に基づく補正を行うことで良好な切り屑の分断を可能とした。そこで周波数・振動幅ごとの振動特性データを記憶するテーブル方式ではなく,図12 に示す2本の近似直線を用いたパラメータ設定方式で振動幅の補正を行うように開発した。図12.振動特性データの近似本対応による振動幅補正の例を図13 に示す。ユーザの指定振動幅が0.040mm の場合,振動特性データからフィードバック振動幅が0.040mm となる振動幅は,0.060mm であることが求められる。そこで差の0.020mmだけ振動幅が大きくなるように補正を行うことで,ユーザが指定した振動幅どおりの振動切削加工が可能となる。図13.振動幅の補正135.むすび工作機械メーカと三菱電機(株)は振動切削加工制御を共同開発し,2014 年に他社に先駆け振動切削加工制御を搭載した工作機械の販売を開始した。不良ワーク減少による開発コスト低減,機械停止回数の減少による生産性向上を実現し,ユーザから高い評価を得て,本制御搭載の工作機械は販売台数を順調に伸ばしている。また,他社CNC メーカに対して優位性を維持するため特許戦略を実施し,関連特許を8件出願。以下の表彰を受賞し,社内外で高い評価を得た。2014 年 優秀発明表彰 (三菱電機)2015 年 中部地方発明賞 (公益社団法人)2018 年 最優秀知財権群賞 (三菱電機)今回開発した振動切削加工制御では,難削材加工のような特殊加工のみに使用される機能ではなく,穴あけ加工,ねじ切り加工などのいろいろなニーズに応えられる機能とすることを重点に取り組んだ。また,振動旋削加工は新しい加工法のため機械メーカ,三菱電機先端技術総合研究所と一体となって開発し何度も改善を重ね製品化した。その過程で従来のNC 制御向けのSW 開発業務から拡大した加工プロセスの開発ノウハウを獲得することができ,提案型業務につなげることができた。今後も三菱電機(株)と協力して,振動切削加工制御の機能拡張・改良に取り組み,競合他社との差別化を図っていく所存である。最後に振動切削加工制御の開発にあたりご支援,ご指導いただいた三菱電機(株)産業メカトロニクス製作所NC システム部の関係各位に感謝の意を表する。参考文献■ 振動切削制御(VCC) 仕様説明書(BNP-C3080-258L)執筆者紹介岩田 好史1986年入社。MITSUBISHI CNCの多軸多系統制御ソフトウェア開発に従事。現在,名古屋事業所モーション・ドライブシステム統括部 NCコア開発部 NC応用開発課 グループリーダー冨田 圭祐2015年入社 MITSUBISHI CNCの多軸多系統制御ソフトウェア開発に従事。現在,名古屋事業所モーション・ドライブシステム統括部 NCコア開発部 NC応用開発課川西 昂弥2018年入社 MITSUBISHI CNCの多軸多系統制御ソフトウェア開発に従事。現在,名古屋事業所モーション・ドライブシステム統括部 NCコア開発部 NC応用開発課