2022年度 三菱電機ソフトウエア技術レポート
ワイヤ・レーザ金属3Dプリンタ「AZ600」専用CNCシステムの開発
1. まえがき
近年、AM(Additive Manufacturing)と呼ばれる積層造形技術が台頭し、3Dプリンタ等の名称で製品化が進んでいる。従来の加工方法に比べ、形状自由度や材料歩留まり等の面で優位性が見込まれる工法であり、今後3Dプリンタ市場の成長(1)が見込まれている。一口に3Dプリンタと言っても造形する素材や造形方式、用途によって様々な種類がある。2022年3月に三菱電機(株)によって製品リリース(2)されたAZ600は、金属ワイヤを素材とし、レーザ光でこれを溶融させて造形する方式(ワイヤ・レーザDED)の産業向け金属3Dプリンタである。粉末金属を素材とする造形方式の製品に比べて、材料歩留まり率の高さ、造形物内部の欠陥の少なさ、造形速度の大きさが特徴である。その造形能力を実現する専用のCNC(数値制御装置)の制御S/W、ユーザインターフェース(UI)画面、CAMの開発を三菱電機ソフトウエア(株)(以下、当社)が担当した。本稿では、AZ600の特徴とそれを実現するCNCシステムについて、制御技術を中心に紹介する。
2. 金属AMについて
AMとは、ベースとなる素材に別の素材を追加していくことで目的の製品形状を実現する製造方法全般を指す言葉である。AMによって製品を製造する装置は3Dプリンタと呼ばれる場合が多い。広い意味では、手作業で行う肉盛り溶接もAMに含まれる。
工作機械やそれに類する自動化装置の観点では、金属を加工するAM(金属AM)は新しい技術である。製造業における省資源、省エネルギー、CO2排出削減などの近年の社会的課題の解決という観点で、金属AMは従来の加工方法にはないアプローチが可能であるとして期待されている。
現在の金属AMの造形方式では粉末床溶融結合(Powder Bed Fusion:以降PBF)方式と指向性エネルギー堆積(Directed Energy Deposition:以降DED)方式と呼ばれる方式が主流である。
PBF方式は造形するための空間全体に金属粉を薄く1層敷きつめる工程と、造形物を作成したい場所だけをレーザや電子ビームなどの熱源で加熱し、部分的に溶融・凝固させる工程を交互に繰り返して造形を進める方法である。
DED方式は造形物を作成したい場所に、金属材料と熱源を投入する方法である。DEDでは材料として金属粉を使うタイプと金属ワイヤを用いるタイプがある。また、熱源としてはレーザや電子ビーム、アーク放電を利用するものがある。
一般にPBFとDEDの比較としてはPBFの方が細かな形状を実現しやすいが、造形サイズを大型化しにくいために小型精密部品向け、DEDは加工速度が速く、装置の大型化が容易なために大型部品向けとされている。
3. AZ600について
本章では、ワイヤ・レーザDED方式の金属3DプリンタAZ600の造形方式と用途を説明した後、加工機の構成、造形制御の特徴、適用事例について述べる。
3.1 緻密・省資源を実現するワイヤ・レーザDED方式
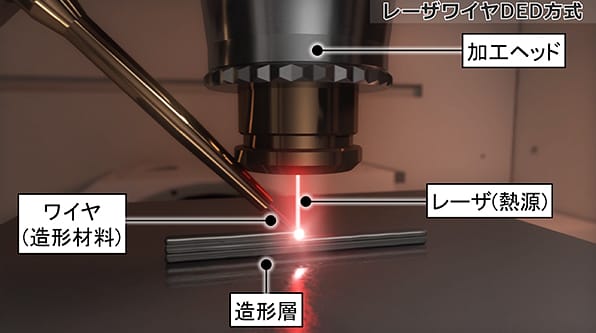
図 1. AZ600の造形イメージ
AZ600では、DED方式を採用しており、材料として金属ワイヤ、熱源としてレーザ光を使用している。本稿ではこれをワイヤ・レーザDED方式と呼ぶ。造形イメージを図1に示す。造形層を積み重ねて立体的な形状を造形する。
ワイヤ・レーザDED方式には以下の特徴がある。
- ・造形物内部に空孔が発生しにくい(緻密)
- ・材料が安価(既存の溶接ワイヤを利用できる)
- ・材料歩留まり率が高い(省資源、安価)
- ・材料供給を細かく制御できる
- ・加工点への熱の投入量を細かく制御できる
ワイヤ方式は粉末に比べて安定加工が難しいという課題があるが、上記特徴と同時5軸制御を精密に協調させることで課題を克服している。その詳細は3.4節に述べる。
3.2 ものづくりの省資源化、省人化、異種金属の一体部品化を実現
AZ600の用途として、従来切削加工で製造していた金属部品を、AMと切削を組み合わせて、より省資源、省エネルギーに製造する用途を提案している。具体的には、AMで製品に近い形状を造形し、切削加工で仕上げて必要な寸法精度や表面性状を得る手法である。全てを無垢材から削り出す場合に比べて材料歩留まり率が向上し、加工時間を短縮できるので、省資源、省エネルギー化を実現できる(2)。加工コストも低下するため、従来切削加工でしか実現できず高価になっていた1点物や少数部品の損益分岐点を低下させ、多品種少量生産のビジネス機会を拡大する可能性も期待できる。
また、摩耗した金型をAMによって補修する用途や、従来手作業に頼っていた溶接工程を金属AMによって代替し、自動化、省人化の需要に対応する用途(3)を提案している。さらに、元となる部品に異なる種類の金属で追加形状を造形することで、異種金属を一つの部品とする用途を提案している(4)。
3.3 加工機の構成
3.3.1 機械構成
機械構成は、XYZ軸方向に移動する加工ヘッドと、造形物を載せて姿勢(傾き/回転方向)を自由に変えられる2軸回転テーブルを組み合わせた、一般的な5軸マシニングセンタのような構成に、ワイヤ送給機構、レーザ発振器を加えた構成になっている。その外観を図2に、主な仕様を表1に示す。
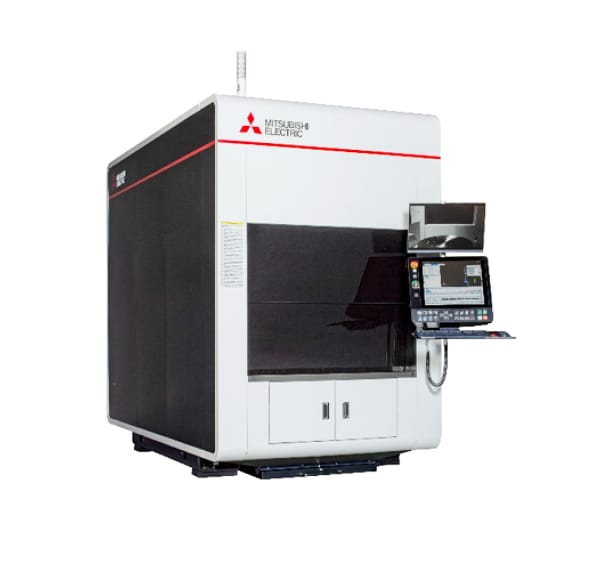
図 2. AZ600の外観
造形方式 | 指向性エネルギー堆積法 (熱源:レーザ、材料供給:ワイヤ) |
|
---|---|---|
外形 | 幅×奥行×高さ [mm] | 1,600×2,900×2,500 |
本体質量 [kg] | 約7,000 | |
軸移動量 | X×Y×Z軸 [mm] | 600×600×600 |
B軸 [°] | ±120 | |
C軸 [°] | 360 | |
ワーク | 最大サイズ [mm] | φ500×500 |
最大質量 [kg] | 500 | |
レーザ定格出力 | 2 kW または 4 kW |
表 1. AZ600の仕様
3.3.2 CNCによりワイヤ送給、レーザ出力を制御する制御ユニット構成
AZ600の制御装置の構成は、CNCを中心とした一般的な切削加工機に用いられる構成に、レーザ発振器の制御ユニットを加えた構成になっている。通常の工作機械ではCNCが各軸のモータを制御するサーボアンプに位置指令を定められた微小な制御周期ごとに送って加工機の動きを制御する。AZ600では同じようにCNCがレーザ発振器制御ユニットに制御周期ごとに制御指令を送る。この構成によって、CNCの制御S/Wによる各軸動作とレーザ発振器の緊密な協調制御を実現している。また、加工ヘッドに搭載されたカメラや各種センサの情報もCNCにフィードバックされる構成になっており、CNCが加工の状態をモニタリングして現在の加工状況に応じてワイヤ送給、レーザ出力を調整できるようになっている。
3.3.3 S/W構成
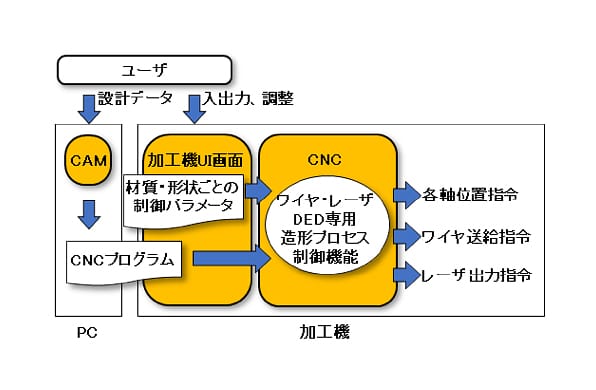
図 3. AZ600のS/W構成
AZ600のS/W構成要素は、主にCNCの制御S/W、加工機UI画面、CAMである。図3にAZ600のS/W構成を示す。
各S/Wの役割をユーザ操作手順に沿って説明すると、最初にユーザは、加工機外部のパソコン(PC)上でAZ600専用のCAMを用いてCNCプログラム(Gコードプログラム)を作成する。専用CAMは、ワイヤ・レーザDED方式特有の制御機能を利用するためのマクロや指令コードを含んだ、AZ600の造形に最適な加工パスを出力する。次にユーザは、加工機UI画面を介して、CNCプログラムや、材料・形状ごとの制御パラメータをまとめた加工条件ファイルを加工機に入力する。最後にユーザが運転を開始すると、ワイヤ・レーザDED専用の造形プロセス制御機能が働き、高速かつ高品質な造形を実現する。
3.4 造形の特徴と制御技術
3.4.1 高精度な点造形と高速な線造形
AZ600の造形では、点造形と線造形の2つの造形方法を定義し、これらを適切に組み合わせて効率的に造形を実施する。表2に、点造形と線造形の比較を示す。
点造形は、軸を停止してその場で点を打つように造形した後、一旦その点が冷却凝固するまで待ってから次の点を造形する手法である。線造形に比べ造形形状の複雑さに関係なく安定して造形でき、精密で酸化の少ない造形物を得られる(5)。ただし、軸の停止時間が長く、全体として加工時間が伸びてしまう。
線造形は、軸を移動しながら線を引くように造形を実施する手法である。加工パスの始終端やコーナ部で造形物の形状が不安定になりやすいが、点造形に比べて造形速度は速くなる。
特徴 | 点造形 | 線造形 |
---|---|---|
安定性 | ◎ | △→〇(造形プロセス制御有効時) |
造形精度 | ◎ | |
造形速度 | △ | ◎ |
表 2. 点造形・線造形の比較
効率的な加工を実現するためには、最大限線造形を活用しつつ、必要な個所では点造形を組み合わせて加工を安定させることが必要になる。一般的に工作機械の軸の軌跡は、CNCプログラムにGコードであらかじめ記載する。AZ600もこの枠組みに従うので、点造形と線造形の選択はCAMでCNCプログラムを作成するときに決定する。AZ600専用のCAMは、線造形を基本としつつ、線造形が苦手な始終端を点造形とする加工パスを自動的に生成する機能を備えている。
3.4.2 線造形を安定化させる造形プロセス制御
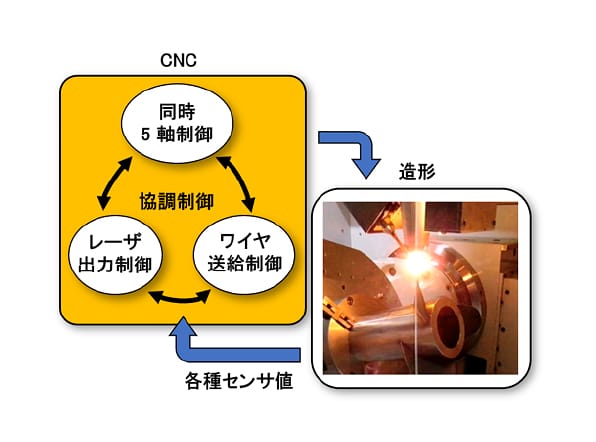
図 4. 造形プロセス制御のイメージ
AZ600では前述のように線造形の苦手な個所を点造形で補って安定加工を実現している。しかし、なるべく線造形を活用した方が加工速度を向上できる。線造形をより安定化させ、適用範囲を拡大するためにAZ600には同時5軸制御とレーザ出力制御、ワイヤ送給制御の協調制御とセンサデータを用いた造形誤差の修正機能からなる造形プロセス制御機能を実装している。(図4)
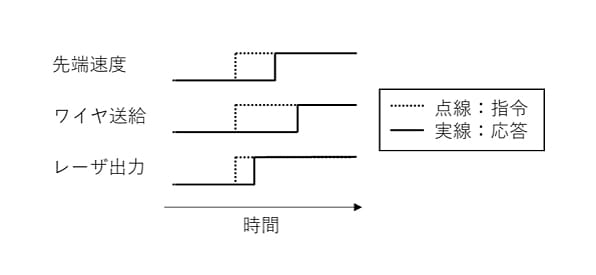
図 5. 各機器の応答タイミングの例
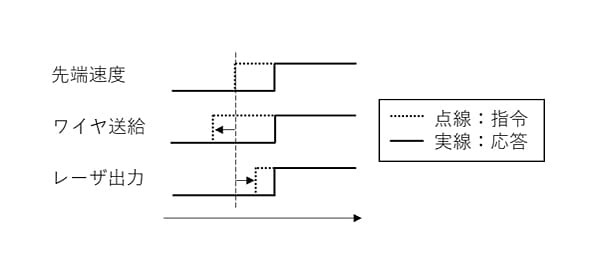
図 6. 先行、遅延指令による協調の実現
- (1)5軸制御、ワイヤ送給、レーザ出力の精密な協調制御
ワイヤDEDでは基本的に、加工ヘッド位置を制御する軸送り速度、ワイヤ送給、熱源の出力が適切な関係にない場合、造形が破綻してしまうことがAlmirらの先行研究(6)によって報告されている。先行研究では熱源に電子ビームを使用しているが、レーザを熱源とするAZ600でも同様である。特に、始終端やコーナのように軸送りが加減速する箇所では、同時5軸制御によって制御される回転テーブル上のワークと加工ヘッドの相対速度(先端速度)の加減速に正確に協調して、ワイヤ送給、レーザ出力を制御する必要がある。しかし、加工ヘッド、ワイヤ送給装置、レーザ発振器は、CNCから指令を受けてから実際にその先端速度、ワイヤ送給、 レーザ出力を実現するまでの時定数に差がある。単純にCNCから同じタイミングで各機器に指令しても、図5に示すように、実際の各機器の応答タイミングは短い時間軸で見るとバラバラになってしまう。図中では、単純化のために矩形的な指令、応答波形で表現している。AZ600の制御では、先端速度の指令に対してワイヤ送給、レーザ出力を少し先行、あるいは遅延させて指令できる調整機能を設けた。図6に示すように、応答のタイミングが合うように調整することで協調精度を向上し、造形を安定化させた。
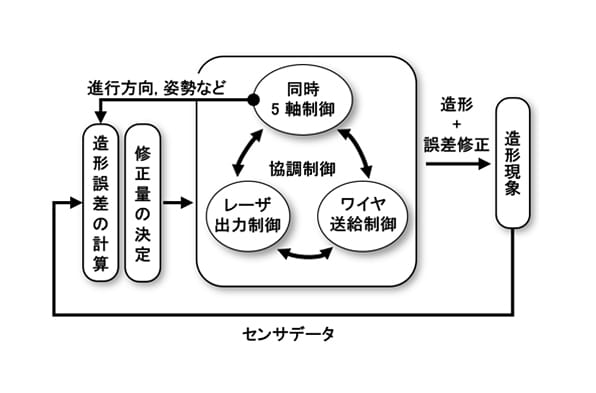
図 7. 造形誤差への対応
- (2)センサデータを用いた造形誤差の修正
先端速度、レーザ出力、ワイヤ送給が理想的な関係に保たれていると仮定しても、造形形状には、溶融した金属の温度や表面張力、重力の影響など、様々な要因が影響するので事前に完全に予測することは困難であり、造形誤差が発生する。特に、高さ方向の造形誤差は、層を重ねるように造形を進めると誤差が累積してしまい、ワイヤの先端と溶融池(レーザが当たって溶融している造形対象)の距離が、安定加工できる一定の範囲から離れてしまう。このような状況では、十分に溶融していないワイヤが基材に衝突したり、溶融したワイヤが溶け落ちたりして、スムーズな造形層を形成できず、造形が破綻してしまう。造形誤差への対応としてAlmirらの先行研究(7)では、カメラとラインレーザを用いて造形物の高さ、幅を計測し、その結果を軸軌跡、ワイヤ送給、熱源の出力に反映させることで単純な直線を積み重ねた壁の造形を安定させる手法が紹介されている。ただし、5軸加工や自由形状の造形を実現するには、カメラやセンサから見た加工の進行方向や姿勢が常に変化するので、カメラやセンサデータだけで造形誤差を正確に計測するのは難しいという課題があった。
AZ600では、5軸加工や自由形状の造形パスでも、カメラやセンサから得られたデータをCNCの同時5軸制御によって計算される進行方向や姿勢などの情報と組み合わせることで正確に造形誤差を計測し、誤差を修正しながら造形する仕組みを実現している。(図7)
この仕組みを用いて、例えば高さ方向の造形誤差が発生した場合、造形誤差によって発生した凹凸に倣うように加工パスを修正して造形の破綻を回避しつつ、造形誤差を修復する方向にワイヤの供給量やレーザの出力、軸送り速度を変化させる制御を実施する。他にも造形誤差を監視、修正する機能を複数組み合わせ、それらを統合して造形プロセス制御機能としてまとめている (3)(4)。
3.5 適用事例
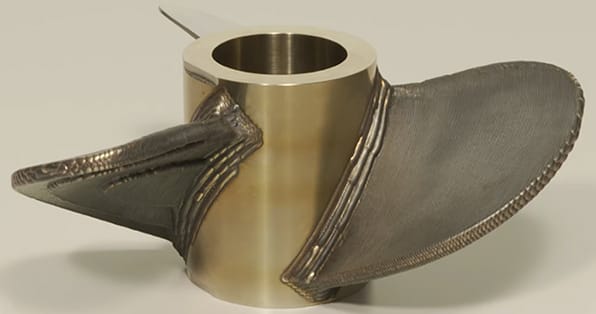
図 8. AZ600で造形したプロペラ
3.4節で述べた制御技術の適用事例として、AZ600でプロペラ形状を造形したものを図8に示す。円筒基材の曲面に、5軸加工となる造形パスで翼を造形した。このプロペラに切削仕上げ加工を施した場合の合計の加工時間は、すべてを無垢材から切削する従来工法と比べて約80%削減できている(3)。
造形時間:8時間47分
造形寸法:Φ300(基材サイズΦ99×L120mm)
造形基材:SUS304
造形ワイヤ:SUS630
4. むすび
金属AMという新しい技術領域の製品AZ600の制御S/Wを開発した。その特徴的な造形方式であるワイヤ・レーザDED方式のAMによる安定加工を実現するために、同時5軸制御とワイヤ送給、レーザ出力の協調制御という難易度の高い機能を実現した。CNC制御、加工機UI画面、CAMと加工機の運用に必要なS/W群を一貫して当社で開発し、製品の実現に貢献した。今後もS/W開発を通してFA分野における社会的課題の解決に貢献していく所存である。
最後に、本開発及び本稿執筆にあたりご指導、ご協力 を頂いた三菱電機(株)レーザ製造部AMシステム設計課の関係者各位に深く感謝の意を表する。
【参考文献】 |
|
---|