2022年度 三菱電機ソフトウエア技術レポート
鉄道車両用空調装置の制御基板集約開発
1. まえがき
鉄道車両用空調装置(以下、空調装置)は三菱電機(株)長崎製作所の主要製品であり、当社は、その空調装置用の制御基板(以下、車冷基板)を開発している。
車冷基板は、様々なタイプの車両に搭載され、車両内外の温湿度情報を取得するため、使用するセンサーの種類が多い。車冷基板のセンサー入力機能は、各センサーの特性に応じて専用の回路が必要である。車両タイプ(注1)ごとに異なるセンサーの種類や数量に対応するため、車冷基板の機種が増え続けていった。
近年、半導体技術が進歩し、限られた条件下で接続センサーを切り替えることができる回路の実現が可能となったため、複数基板を集約した車冷基板を開発した。回路追加によって部品点数が増加したが、A/D変換手法を工夫することで省スペース化を実現し、従来の基板サイズのまま、複数基板の集約を実現した。
これにより、センサーの種類・数量が異なる車両タイプにも基板の適用が可能となり、機種の増加を抑えることができた。
本稿では、基板集約のために採用した切替回路とA/D変換手法について紹介する。
- (注1)車両タイプ:鉄道車両の種類。鉄道会社の違いや通勤電車、豪華列車などの用途の違いにより、多くの種類が存在する。
2. 車冷基板の概要
2.1 空調装置の概要
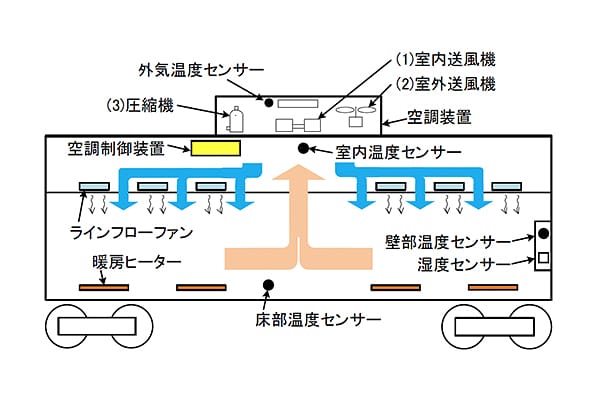
図 1. 車両内の空調装置の機器構成
車両内の空調装置の機器構成例を図1に示す。
空調装置は、次の機器で構成されている。
- (1)室内送風機
- (2)室外送風機
- (3)圧縮機
空調装置は、冷凍サイクルの原理により、冷房を行っている。圧縮機により圧縮した冷媒ガスを循環させ、室外送風機により車内の熱を車外に排出し、室内送風機により車内に冷風を吹き出す。
空調装置を構成する機器の台数は、車両タイプにより異なる。また、室内送風機、室外送風機、圧縮機の台数増減に伴い、使用されるセンサーの種類や数量も変わるため、車両タイプに応じた車冷基板が必要となる。
2.2 車冷基板の構成
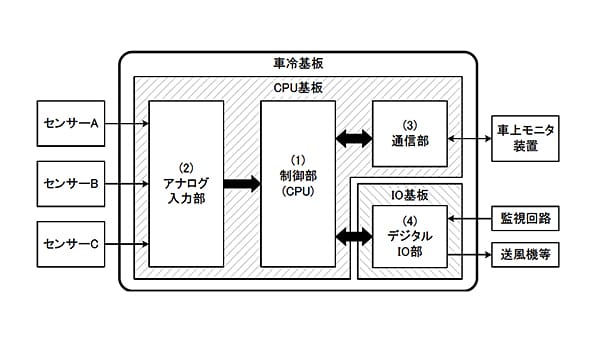
図 2. 車冷基板のブロック図
車冷基板は、空調制御ソフトウェアを搭載し、空調制御装置に据え付けられる。車冷基板のブロック図を図2に示す。
車冷基板は、以下で構成されている。
- (1)制御部(CPU)…各種機能を統括する
- (2)アナログ入力部…各種センサーの情報を読み取る
- (3)通信部…車上モニタ装置との情報交換を行う
- (4)デジタルIO部…空調装置の機器を監視制御する
本稿で述べる車冷基板は、デジタルIO部を搭載した基板(以下、IO基板)と、制御部、アナログ入力部、通信部を搭載した基板(以下、CPU基板)に分かれている。
IO基板は、車両タイプごとに異なる車両内電源の種類と入出力の信号数に対応するため、十数機種の基板が存在する。また、CPU基板は、車両タイプごとに異なるセンサーの種類と数量に対応するため、アナログ入力部が異なる基板が8機種存在する。
IO基板は、複数電源対応の部品がないため集約できない。一方、CPU基板は、以下の2つの課題を解決できれば集約が可能である。
- (1)アナログ入力部の複数センサー対応
- (2)基板サイズの維持
課題(1)は、切替回路を追加することにより解決できるが、従来の切替スイッチは高価でサイズも大きく、実現できていなかった。近年、高性能でサイズも小さく、低価格の部品が登場したため、実現することができた。また、切替回路の追加に伴い、課題(2)が浮上したが、A/D変換手法を工夫することで省スペース化を実現することができた。
3章では、これら課題への対応について説明する。
3. CPU基板の集約
3.1 従来の仕組み
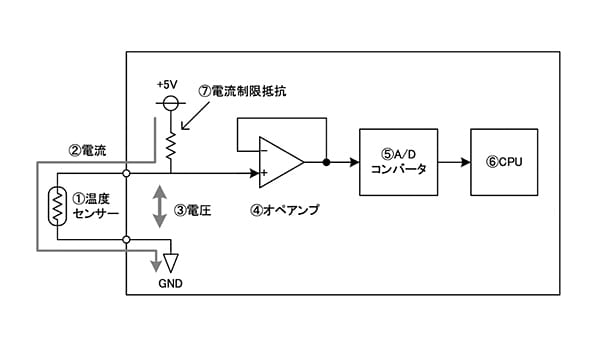
図 3. アナログ入力部の回路
アナログ入力部の複数センサーの一つに温度センサーがある。温度センサーとは、温度により抵抗値が変化する性質の部品であり、0℃~40℃を0Ω~6kΩで示すものや、0℃以下から60℃以上の温度を0Ω~100kΩで示すものがある。前者は、車両内などの常温環境で使用され、後者は外気や低温地域、温暖地域などの特殊環境で使用されている。
アナログ入力部の回路を図3に示す。温度センサー(図3①)の抵抗値は温度によって一意に定まるため、車冷基板から温度センサーに一定の電流(図3②)を流すことで、温度センサーの抵抗値を電圧(図3③)として検出する。検出した電圧はオペアンプ(図3④)を用いたボルテージフォロワ回路(注2)を介し、A/Dコンバータ(図3⑤)にてデジタル信号に変換後、CPU(図3⑥)に受け渡している。
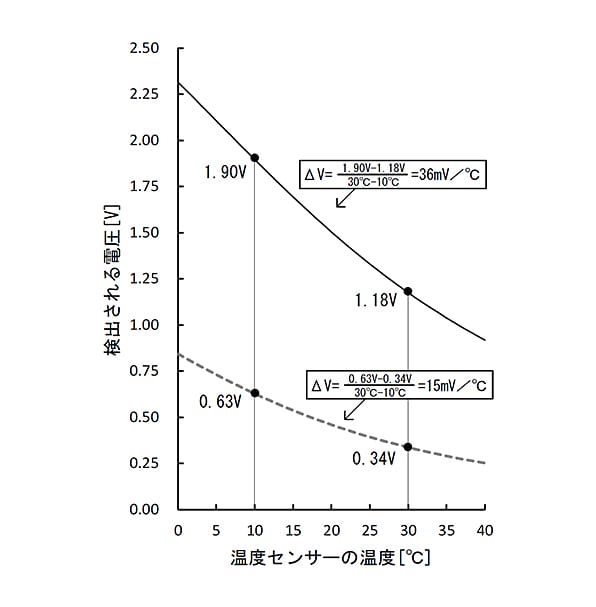
図 4. 検出される電圧の特性グラフ
ここで、アナログ入力部で検出される電圧の特性グラフを図4に示す。
使用する温度センサーの特性と電流値の整合がとれている場合は、図4の実線のように1℃当たりの電圧変化が大きくなり、温度換算精度が細かくなる。
一方で、温度センサーの特性と電流値の整合がとれていなければ、図4の破線のように1℃当たりの電圧変化が小さくなり、温度換算精度が荒くなる。
例えば、10℃~30℃の範囲を測定する場合、実線では1.90Vから1.18Vの範囲、点線では0.63Vから0.34Vの範囲で電圧として検出する。前者は1℃当たり36mV電圧が変化するが、後者は1℃当たり15mVしか電圧が変化しないため、前者の方が温度の変化を精度よく取得することができる。
したがって、従来は使用する温度センサーの特性に合った電流制限抵抗(図3⑦)を車両タイプごとに選定していた。
- (注2)ボルテージフォロワ回路:入力電圧と出力電圧が等しくなる回路。入力インピーダンスが高く、電流がほとんど入力されないため、前段回路の電圧を正確に再現できる。後段部品(A/Dコンバータ)の入力インピーダンスの影響を受けないようにするバッファ回路である。
3.2 切替機能の追加
アナログ入力部を複数の温度センサーに対応させるには、接続する温度センサーの特性に合わせてスイッチで電流制限抵抗を切り替えることができる回路にすればよい。
基板に実装するタイプの代表的なスイッチの種類と特徴を表1に示す。
メカニカルスイッチは単純な回路で切替を実現できるが、微弱電流時に接触不良が発生する恐れがある。温度センサーは、温度が低くなると抵抗値が上昇し、微弱電流となるため、採用は望ましくない。
半導体スイッチであれば、微弱電流で使用可能であるため、一般的に使用されているアナログスイッチICの採用を試みたが、部品サイズが大きく、加えてオンしたときの抵抗値(以下、オン抵抗)が小さいものは高価なため採用できなかった。
そこで、オン抵抗が小さく小型で低価格のMOSFET(注3)で切替回路を実現することにした。
- (注3)MOSFET:Metal Oxide Semiconductor Field Effect Transistorの略称。半導体スイッチの一種。モスエフイーティーと読む。
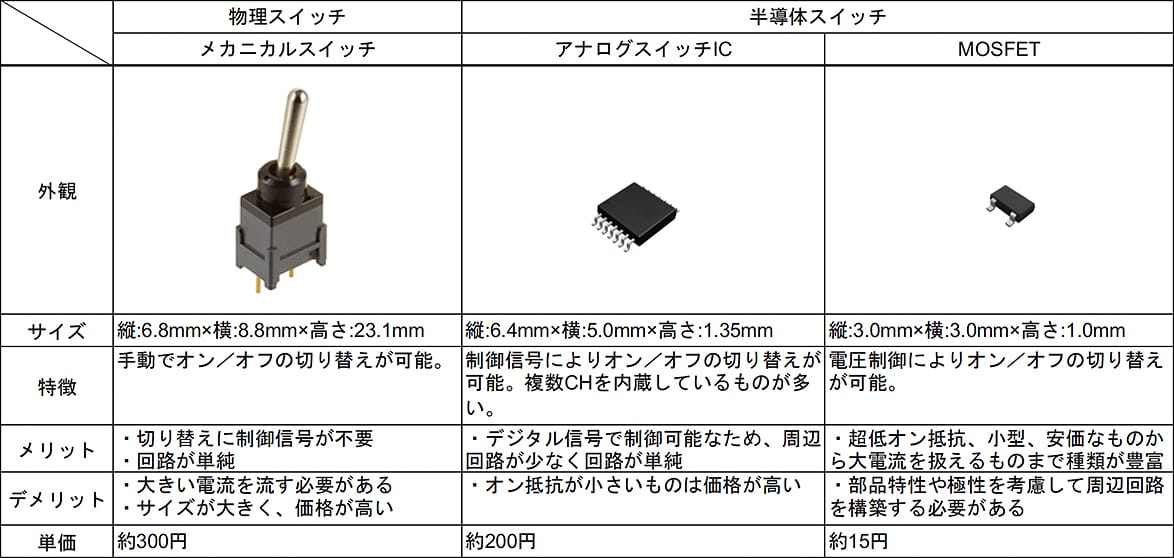
表 1. スイッチの種類と特徴
- (1)MOSFETを使用した切替回路
新しくMOSFETを使用したアナログ入力回路を図5、図6に示す。この回路は、電流制限抵抗が12.2kオームで最適である温度センサーAと4.7kオームで最適である温度センサーBの接続に対応する切替回路である。図5は温度センサーA対応時の動作、図6は温度センサーB対応時の動作を示している。
温度センサーAを接続する際は、切替信号の出力を空調制御ソフトウェアでHighレベル(図5①)に設定し、MOSFETをオフ状態(図5②)にする。電流が図5③の経路で流れるため、7.5kオームと4.7kオームの合成抵抗である12.2kオームで電流制限がかかり、温度センサーAの接続に適した回路となる。
一方、温度センサーBを接続する際は、切替信号の出力をLowレベル(図6①)に設定し、MOSFETをオン態(図6②)とする。電流がMOSFETに流れる(図6③)ため、電流制限抵抗は4.7kオームとMOSFETのオン抵抗の合成抵抗となる。オン抵抗が十分に小さければ、温度センサーBの接続に適した回路となるため、オン抵抗が極力小さいMOSFETを選定する必要がある。

図 5. 新アナログ入力回路の動作(センサーA対応時)
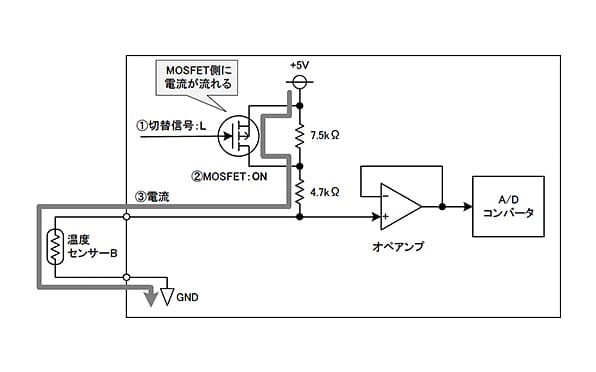
図 6. 新アナログ入力回路の動作(センサーB対応時)
- (2)電圧検出精度を考慮した部品選定
アナログ入力部では、数mVの微弱な電圧差を検出するため、MOSFETと電流制限抵抗は誤差が小さい部品を選定する必要がある。
車冷基板の仕様である温度取得誤差±0.5℃以下を実現するには、電圧検出誤差を15mV以下に抑える必要があるため、オン抵抗が0.5Ω以下のMOSFETが必要であった。そこで、オン抵抗が最大でも0.12Ωと小さく、かつ小型のMOSFETを選定した。
また、MOSFETは、部品により動作電圧などの特性が異なるが、CPUの出力信号で直接駆動可能な特性をもつMOSFETを採用することで、切替回路の規模を最小限とした。
電流制限抵抗も誤差が±1%のものから±0.05%のものに変更し、電圧検出精度の向上を図った。
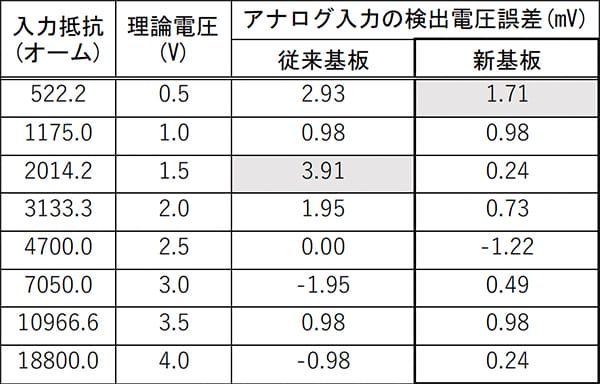
表 2. 新基板と従来基板の検出電圧誤差の比較
- (3)新基板と従来基板の検出電圧誤差の比較
新しいアナログ入力回路の実機検証を行った結果を表2に示す。検証は、可変抵抗を接続し、温度センサーを模擬した入力を与え、新基板と従来基板の検出電圧誤差を比較することにより行った。
その結果、新基板の検出電圧誤差は最大1.71mVとなり、目標の検出電圧誤差15mV以下を達成した。また、従来基板の検出電圧誤差は最大3.91mVであったため、新基板は従来と同等以上の精度を確保しつつ、機能を集約することができた。
3.3 省スペース化の実現
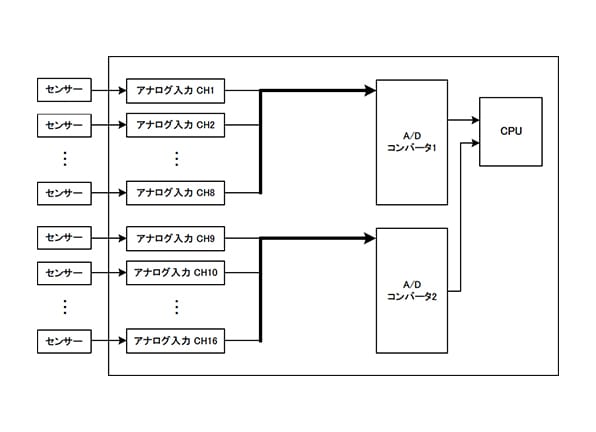
図 7. 従来のA/D変換回路
MOSFETを使用した切替回路の追加により、従来基板から部品点数が増加した。基板の外形サイズを従来基板に合わせるために、大型部品であったA/Dコンバータを2個から1個に削減することを検討した。
従来のA/D変換回路は、図7に示すとおり、16CHのセンサー入力を8CH入力のA/Dコンバータ2個に割り付けて使用していた。
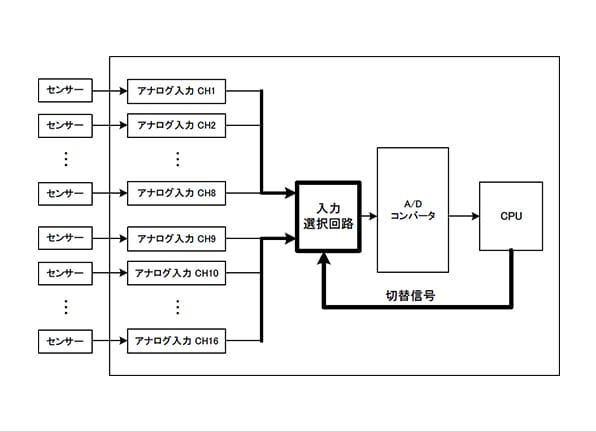
図 8. 新しいA/D変換回路
図8に示すとおり、CPUからの切替信号により、CH1~8とCH9~CH16を選択できる回路を追加した。A/Dコンバータへの入力を切り替えながら時分割で2回A/D変換することで、8CH入力のA/Dコンバータ1つで16CH分のA/D変換が可能となり、省スペース化を実現した。
本A/D変換手法はCHを切り替えながら時分割で変換を行うため、A/D変換の処理時間が2倍になるが、取得する情報は温度や湿度であり、短時間で急激に変化する情報ではないことから、処理時間を要しても問題はない。
3.4 機能集約した新基板の仕様
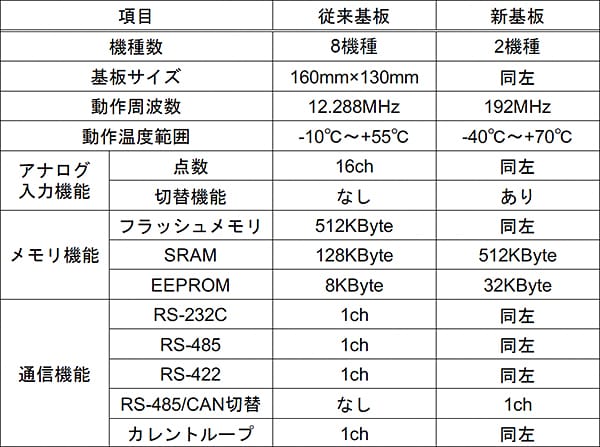
表 3.従来基板と新基板の仕様
表3に従来基板と新基板の仕様を示す。センサー切替機能を追加した新しいアナログ入力回路を構築することで、8機種あった従来基板を2機種に集約した。
新基板は従来基板と外観上の大きな差異はないため、更新工事の際に従来と同じ手順で基板設置やケーブル接続が可能である。
さらに、アナログ入力機能だけでなく、CPUの動作周波数や、動作温度範囲、メモリ機能、通信機能についても、従来より性能を向上させており、より多くの車両タイプへの適用が可能となった。
4. むすび
今回の開発では、切替機能を搭載したアナログ入力回路と部品数削減のためのA/D変換手法を考案し、複数基板の集約を実現した。
今後の基板開発でも、これまでの基板開発で培ったノウハウを活用し、使用条件の違いに対応できる回路を提案することで、派生基板の増加を抑制し、原価低減を図っていく。また、部品の進化に追従しながら、より良いハードウェア製品を開発していく所存である。
最後に本開発に当たり、技術的な助言をはじめとして、様々な面でサポートいただいた関係者の方々に深く感謝申し上げる。